What’s New in Altair AcuSolve 2021.2
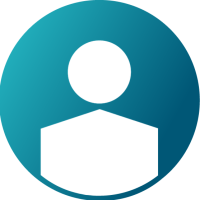
What’s New in Altair AcuSolve 2021.2
EDEM Coupling: Non-spherical Particle Lift and Torque Models
Particles in EDEM / AcuSolve coupling can vary from glass beads to small rocks, to leaves, straw, and grass, to tablets and fine powders, and more. Many of these types of particles are non-spherical in nature and when they interact with a surrounding flow field the aerodynamic forces applied should account for their shape. With version 2021.2 EDEM / AcuSolve coupling now supports new models for lift and torque specifically designed to model non-spherical particles more accurately.
The first of the new lift models, nonspherical_lift, includes the effect on lift due to the orientation of the particle relative to the oncoming flow. The second model, Saffman_Magnus_nonspherical_lift, additionally accounts for lift generated due to shear in the ambient flow, known as the Saffman lift force, and lift generated due to particle rotation in a free stream flow, known as the Magnum lift force. The Saffman component of lift will greatly improve the accuracy of particles being lifted off wall boundaries and the Magnus component of lift will improve the accuracy of the motion of particles under rotation.
Three new torque models have been added for 2021.2 as well. The first model, pitching_torque, also known as “offset torque”, is the torque due to the cumulative effect of lift and drag forces acting on the center of pressure of the particle. The second model, rotational_torque, also known as “rolling friction torque”, models the torque about the primary axis of the particle. The third model, pitching_rotational_torque, is, as the name suggests, a combination of the first two torque models.
Non-spherical lift due to particle orientation | Saffman lift due to local shear flow | Magnus lift due to particle rotation |
Pitching torque | Rotational torque | Pitching and rotational torque |
EDEM Coupling: Lift and Drag Scaling
Industrial-level simulation is commonplace for today’s CFD analysts and the need to supplement physical testing with accurate full-scale modeling has never been greater. Particle modeling, of dust and powders, for example, involved in simulation at this scale can pose real challenges directly impacting the computational and turn-around times. When faster delivery of these types of results is necessary EDEM / AcuSolve coupling provides the capability to agglomerate particles while maintaining the impact on overall momentum. The net effect is a reduction of the number of particles and consequently turn-around time. To maintain an equivalent net impact on the fluid due to the presence of agglomerated particles users can set the edem_force_scale_factor parameter.
Particles modeled discretely | Particles agglomerated with scale factor |
EDEM Coupling: Particle Mass Transfer
Spray technology is used in a wide variety of manufacturing processes, from thermal management to enhance cooling, to inhibit mold growth during food processing, or to apply coatings. With EDEM/AcuSolve coupling the spray process occurs within EDEM, depositing spray particles on surfaces. The accumulated liquid volume is tracked on each particle during the spraying phase simulation. The heat and mass transfer of drying and cooling occurs during the coupled simulation.
Spray accumulation on particles with heat and mass transfer
Topology Optimization
What is the most efficient path to deliver your fluid from point A to point B? How do you shape your duct or manifold without inadvertently negatively impacting the design? The space you have in which to package this design can be very convoluted. And worse yet, what do you do if, or rather when, your package space changes? All these issues can be addressed with AcuSolve’s new topology optimization feature. Offered in v2021.2 and available through the SimLab interface, AcuSolve’s latest solver-integrated optimization feature gives you the power to be your own Simulation Sculptor.
In the hypothetical scenario below our engineer is tasked with designing a manifold that will deliver fluid from the single inlet at the top to the four outlets at the bottom. Her package space has been interrupted by another carry-over component that cannot move. With AcuSolve and SimLab she can quickly and easily select her design and non-design volumes, specify an inlet with flow rate and her outlets, and run. The nice symmetric shape that meets her optimization criteria of minimizing the required mechanical energy is shown in the left image below.
On a similar but variant program, her colleague is faced with the same problem. He must also deliver the fluid from point A to points B1 through B4 in the most efficient way but in this program variant, the package space is slightly modified, and no longer symmetric. After hearing of the ease and success with which his colleague created her manifold, he decided to do the same. With the option of either picking up where his colleague left off or starting with his own model, he was also able to quickly and easily arrive at the non-symmetric manifold shape shown in the right image below.
In each scenario the process is simple: define and select a package space that is a valid space for your final design to exist. Optionally, you may select non-design volumes which will not be considered in the topology optimization step. Next, identify inlets and outlets with appropriate flow rates and run. The shape will then emerge from the design space.
Topology optimization, original design space | Topology optimization, alternate design space |
Porous Media Physical Velocity
There are many different useful applications of a porous media model in computational fluid dynamics. In general, a porous media model is used when the geometric modeling would be too cumbersome or costly. If the effect on the surrounding larger flow field is needed but not the details of the internal flow, then a porous media model is the proper choice. It is common to model filters or screens as porous media but other components such as grilles, or lattice-like structures are also likely candidates. By default, AcuSolve will solve for the superficial velocity associated with the specified pressure drop information and modeled geometry. This is the velocity based on Darcy’s Law which states that the flow rate is proportional to the pressure gradient. What is calculated is essentially the change in velocity, in the flow direction, as if it only experienced the pressure gradient. However, the actual path taken by the fluid on the interior of the porous medium can be quite different and chaotic. The porosity of the material defines the fraction of fluid space to solid space by volume. The smaller the number the potentially more tortuous the path for the fluid to follow. This additional ground to cover by the fluid and constriction in the flow path will result in higher internal flow speeds. This is what is termed physical velocity.
The superficial velocity through the porous medium is shown in the first image. The second image shows the accelerated physical velocity for a porosity of 0.4. The plot shows the pressure drop through each model. The pressure drop is the same through each because the same pressure drop vs flow rate information was used for both.
Superficial velocity through a porous medium | Physical velocity through a porous medium |
Centerline velocity through a porous media