Designing Rib Stiffeners the Easy Way with AUTORIB
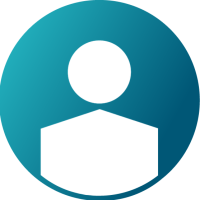
Product = Design Studio
Rib stiffeners are commonly used to strengthen plate and shell structures. The benefit of the ribs strongly depends on the location and pattern of the ribs. In general, adding ribs will add stiffness, but they also add material and thus, increase the cost. It is desirable to only add material in the places where it will be most effective. GenesisÒ Structural Analysis and Optimization software include tools to help design rib patterns. As an example, consider a component cover:
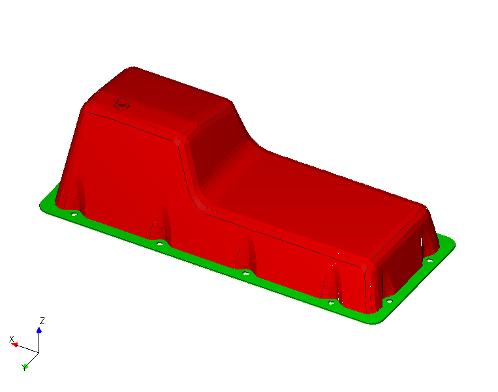
This cover will be subjected to dynamic loading and will vibrate in response. It is desirable to keep the lowest natural frequency above 350Hz. Without any rib stiffeners, the lowest mode is 303Hz, and so is not sufficient.
The unique AUTORIB capability of Genesis will automatically create candidate rib stiffener elements on the model along every edge of the existing mesh.

The generated rib elements look like this:
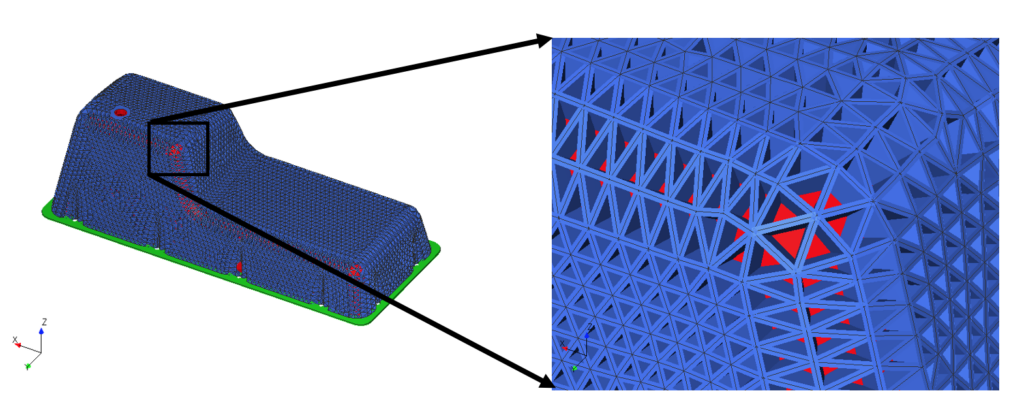
Topology optimization can be used to determine the best subset of the candidate ribs that minimizes added mass while reaching the frequency target.
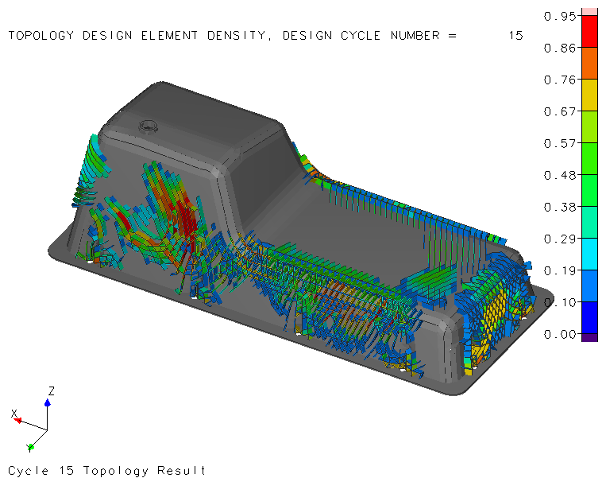
While these results are valuable, they illustrate a common difficulty when using topology optimization with dynamic responses, namely, that the final results are often not well polarized. Another unique feature of Genesis can be used to overcome this difficulty: TSELECT. Once we have determined the lowest mass fraction needed to meet the frequency constraint, we can add TSELECT data to force the results to polarize.
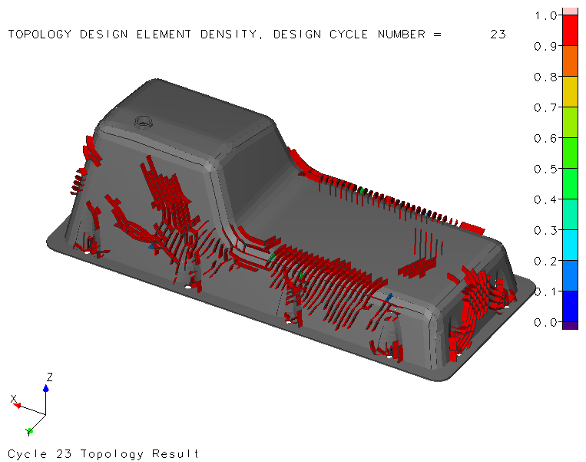
Now we have a very clear indication of the best locations and patterns for the rib stiffeners. For more information about AUTORIB and TSELECT, please leave a comment below.