romAI & nFX: Leveraging AI on Drivetrain CFD Simulations
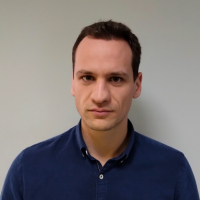

Abstract
In this article we discuss how romAITM can help to efficiently predict the thermal behavior of gearboxes during operations smartly reusing data from nanoFluidXR oil flow simulations. To solve the thermal problem, a dynamic non-linear Reduced Order Model (ROM) is generated to estimate the Gear-Oil heat transfer coefficient (HTC) based on variable gearbox RPM & Oil fill level.
Introduction and problem statement
During real-life scenarios, drivetrains operate in varying conditions such as: RPM, orientation (tilt & pitch), oil fill level, oil grade/viscosity. All these variables affect the oil distribution and thus how heat is exchanged.
To characterize the system, meaning the effect of these variables, one would typically need to run a lengthy design of experiment (DoE) such as a Full Factorial and then approximate the response with a Look-up table. The issue with this approach is that quickly the size of experiments become too large to solve in reasonable times even with HPC’s. Moreover, by using a Look-up table you limit the prediction to only steady state scenarios (LuT is a static function) thus missing the transient response hence the most realistic and common condition during operations.
To solve the issues mentioned above, we leverage romAITM that allows us to create a dynamic Reduced order Model with AI. Compared to the previous LuT approach, we now consider the states of the system (memory effect) and approximate the non-linear response with few data. This generated ROM can then be either directly used “As is” in an optimization process, or it can be integrated into a system simulation to do further analysis. For this example, we will explore the later approach.
Workflow
As already discussed, to estimate the heat transfer the Gear-Oil HTC must be calculated. By using the results from the nanoFluidXR oil flow simulations we train / generate a ROM with romAITM that estimates the HTC as a function of RPM & Oil fill level. This estimation is then used as an input into a lumped parameter thermal model represented in AltairR Twin ActivateTM, our systems integration platform.
nanoFluidX Simulations and Data Generation
nanoFluidXR (nFX) is a CFD simulation software particularly suitable for drivetrain oiling simulations. That is because the solver is based on the Smoothed Particle Hydrodynamics (SPH) method instead of the traditional Finite Volume (FV) method. The SPH method is a mesh-less method making it ideal for high-deformation type of flows with complex moving geometries. More info about the SPH method and nFX can be found on the article here The Smoothed Particle Hydrodynamics Method vs. Finite Volume Numerical Methods (altair.com).
In this example we simulate the gearbox of an electric vehicle and calculate the HTC integrated over the area of the input, middle and output shaft.
To be able to characterize the response we need training data. Instead of going with a full factorial DoE, we chose a central composite design which allows to save 4 training runs (5 runs instead of 9) since we only consider the effect of RPM / Oil Level for this “simplified” model. Considering that each nFX run takes ~8h for 2s of transient simulation, this translates into a total of 32h saved.
While this may not initially look like a lot, in the full problem definition (including orientation & oil grade) the runs savings would easily translate to a few hundreds of hours.
On the figure bellow we present the training scenarios definition and HTC results. Notice that we have included a separate Test set. This will be used to validate our model and test the generalization capability.
Reduced order model (ROM) generation with romAITM
Each transient nFX run generates hundreds of valid training points that can be used during the training process. All the 5 training runs are concatenated into a single csv file, whose 1st column is the time vector while the other columns are the inputs, outputs, and states of the romAI model.
We then feed the training file into the romAI GUI (accessible from Twin ActivateTM), starting with the Pre-processor tab where we can preview and possibly filter the data when handling dynamic systems. Next, we move on to the Builder tab where we set up the system structure and define the hyper-parameters used during the training. Usually very few parameters need to be tuned to create a good romAI model.
But what makes a good romAI model? First, the model needs to be accurate in terms of errors on the prediction. Moreover, the model needs to generalize well, meaning to have a good response when tested with unfamiliar inputs. To quickly evaluate these, we can leverage the post-processor tab, or deploy the romAI model into Twin ActivateTM and perform a time-simulation there.
In the figure below we evaluate the prediction on the training set (data we used to train the model) & test set (data we excluded from training to test the generalization)
ROM Deployment on Thermal system
One of the main advantages of romAI is that the model generated is dynamic, so it can be easily integrated into the rest of your system for further analysis. The romAI can be deployed natively into Twin ActivateTM or exported as a FMU (Functional Mock Up), or even C code to be used in 3rd party solutions.
For our purposes we will use the first approach and couple it with a 1D lumped-parameter thermal model constructed with thermal components from the Modelica library. Twin ActivateTM has a wide variety of pre-built blocks and models built with the Modelica language, however the advanced user can create/develop more complex components on his own.
To create the thermal model a “heat exchenger” and a “HeatCapacitor” block are used in combination with sensors to measure the average temperature of components and heat flow. The temperature of oil / metal is set as initial condition. The model can give a good indication of the heat transferred, especially considering that the HTC integrated over the area of components is estimated accurately from high-fidelity simulations.
Finally, we run the combined system simulation on the unfamiliar test case and get the results for the Heat Flow and Gear Temperature along time
Note that this simulation only takes 0.2s of CPU time to run, so for this example the time-gain factor is more than 130.000!
Conclusions
- Relatively few nFX transient simulations needed compared to traditional approaches.
- Gain Factor > 130.000 enabling 1-D Analysis, Real Time applications & Optimization
- Able to predict dynamic response, not just the final steady state value
- Very good generalization capabilities
If you are interested in more applications regarding romAI check out these links: