Using Altair Embed® to Develop a Battery Management System for Electric Vehicle Applications
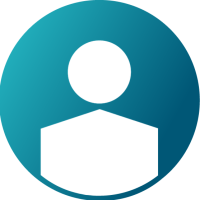
Using Altair Embed® to Develop a Battery Management System for EV Applications
Anthony Boon
Digital Power Consultant for Altair
Summary
The steps performed to develop a battery management system (BMS) demonstration for EV applications are outlined. Three application examples are given, differing by their hardware implementation, starting from the initial experimentation to the routine development and on to a final production-ready design:
- BMS system set-up connected directly to the Embed GUI using real-time serial communication.
- BMS system set-up using a microcontroller board performing the real-time communication, control, and monitoring functions while connected to the Embed GUI.
- BMS system set-up using a central microcontroller and CAN communication with a vehicle control unit (VCU).
Introduction
Battery Electric Vehicles (BEVs) are becoming ever more popular and in high demand. The most critical and costly element of the BEV is the battery system. In order to guarantee optimal performance, it is important to continually monitor the battery pack and the enclosed cells connected in series under all driving conditions and during battery charging.
The charging is required to occur in ever shorter intervals and at higher power, placing more stress on the battery if not managed correctly. The battery needs to be maintained in optimal condition to guarantee the maximum mileage range and life expectancy, by monitoring and controlling the equalization of the many cells in series, while maintaining the operating temperature of the battery pack within limits.
Balancing the cell voltages during charging is necessary in order to equalize the charge applied to the cells, therefore maximizing the available state-of-charge (SOC) of the battery pack. Balancing the cell voltages also aids in maximizing the lifetime and optimizing the performance over that lifetime, thereby maximizing the so-named state-of-health (SOH) of the battery pack.
The following BMS demonstration uses the bq76PL455EVM evaluation module (https://www.ti.com/tool/BQ76PL455EVM) from Texas Instruments (TI) as shown in figure 1.
Figure 1: Texas Instruments bq76PL455EVM evaluation module.
The TI bq76PL455EVM evaluation module supports from six to 16 cells in series, and up to six bq76PL455EVMs can be connected in a series configuration for a maximum of 96 cells in series (96S). However, the bq76PL455-q1 BMS chip of the evaluation module supports up to 16x16 cells in series (256S).
The evaluation module requires a flexible battery setup in order to verify the configurability and robustness of the developed algorithms. For this reason, the battery board as shown in figure 2 was developed to connect directly to the TI bq76PL455EVM.
Figure 2: Battery board developed to evaluate the bq76PL455EVM together with Altair Embed.
The battery board supports from one to 16 type 18650 cells connected in series. Other battery boards can be connected in series (or parallel) for higher battery pack voltages (or capacity), together with multiple bq76PL455EVM evaluation modules (figure 9).
Application example 1
In this first application example, the TI bq76PL455EVM evaluation module is connected directly to the PC via a real-time serial interface. The bq76PL455EVM is powered by eight LiFePO4 cells mounted in a series configuration on the battery board. The LiFePO4 cells have a nominal voltage of 3.2V and are charged at a nominal charge voltage of 3.6V/cell.
Figure 3: BMS setup with 8 series cells connected to a charger/load. The serial communication interface of the bq76PL455EVM is connected directly to the PC running the Embed GUI.
The communication, monitoring, and control routine is performed in the Embed diagram running on the PC, which also forms the GUI of the battery monitoring system in this first application example. The Embed GUI reports all cell voltages, selected cell temperatures, alarms, balancing, and status of the BMS system and battery by constantly polling the bq76PL455EVM BMS module. Some pages of the Embed GUI developed for this system are shown in figure 4.
Figure 4: Example pages of the Embed GUI.
The BMS system is completely configurable using the Embed GUI, as shown in figure 5.
Figure 5: Examples of the Embed GUI available configuration dialogs.
The Embed GUI accurately reports the current condition of the battery pack and the BMS system and balancing. The GUI is also configurable for logging data and can be easily modified for customer-specific applications using the Embed IDE.
Figure 6a: Cell voltage imbalance after charging with balancing disabled. Figure 6b: Cell voltage balance after charging with balancing enabled.
Figures 6a and 6b compare the results of charging with balancing disabled and balancing enabled. Any small difference in the initial state of the battery cells and, in particular, the SOC of each individual battery cell causes differences in the cell voltages toward the end of the charging cycle. Even if initially small, these differences will increase over time after many discharge-charge cycles. Without cell voltage balancing, the result is an imbalance in the SOC of the cells, causing the battery pack as a whole to not be optimally charged and therefore not provide the optimal mileage range. Also, the charge imbalance can cause detrimental effects in the battery cells during use, decreasing the lifetime of the battery pack. In the worst case, catastrophic failure of one or more cells due to severe overcharging can occur.
The majority of the imbalance in the equalization of the cells normally occurs above 90% of SOC toward the end of charging and for this reason, the charging may be terminated at 90% of SOC to help prevent overcharging of individual cells. Similarly, the battery may be shut down from discharge during driving when the SOC reaches 10% in order to protect against over discharge (reference 4). This results in a nonoptimal mileage range due to the inability to utilize 100% of the battery capacity. A correctly balanced battery, along with an accurate SOC determination can optimize the SOC limits for the cut-off of the charger, as well as the battery when in discharge.
The BMS system also monitors cell temperatures, which are particularly critical during rapid charging. If a cell temperature begins to rise unexpectedly, an appropriate action – such as reducing the charging rate or switching off the charger – must be immediately taken. By controlling the battery temperature with the cooling/heating system, together with the monitoring of the cell temperatures, the available mileage range can be optimized because the available battery capacity is temperature dependent.
Comparator thresholds are completely configurable for all cells and actions can be taken depending upon the type of event or measurement performed.
Application example 2
In this application example, the TI bq76PL455EVM evaluation module serial interface is connected to the TMS320F28379 microcontroller mounted on an experimenter kit baseboard (https://www.ti.com/tool/TMDSDOCK28379D). Communication with the bq76PL455EVM and the necessary BMS operations are now performed directly in the microcontroller, while the microcontroller communicates the data to the Embed GUI via the JTAG interface. The use of the JTAG interface together with the Embed IDE significantly improves debugging the BMS communication, control and monitoring software when compared to other development environments.
The battery pack configuration selected in this example has 16 series 18650 Li-Ion cells that are charged at a nominal 4.2V/cell. The configuration is shown in figure 7.
Figure 7: BMS setup with a Texas Instruments TMS320F28379 microcontroller interfaced directly to the EVM.
The internal control block in the Embed GUI diagram of application example 1 is code-generated and compiled for the selected microcontroller using the compound block edge pins for data exchange. The generated OUT file is then linked in a target interface block to run the entire application in the microcontroller RAM. The Embed GUI, in this case, communicates with the microcontroller over the JTAG interface. The microcontroller communicates directly with the bq76PL455EVM over the serial interface. The microcontroller also measures the battery pack voltage and current through a direct connection to the battery board, which is used for the determination of the SOC.
Figure 8: Embed GUI applied to Application Example 2.
This application can be easily expanded to more cells in series for higher battery voltages, using multiple battery boards and bq76PL455EVM modules. An example is the 32 cell, series configuration (32S) as shown in figure 9.
Figure 9: BMS setup with stacked EVMs and battery boards for higher battery voltages (in this case with a nominal battery voltage of 134.4V).
In this case, EVM2 is also enabled in the Embed GUI resulting in the population of the cell voltages and temperatures for cells 17 to 32, as shown in figure 10.
Figure 10: Embed GUI for Application Example 2 with EVMs 1 and 2 enabled for up to 32 series cells.
Application example 3
In this application example, the TI bq76PL455EVM evaluation module is connected to the microcontroller as in application example 2; however, the routine has been programmed into the non-volatile flash memory of the microcontroller and the BMS control routine can operate independently. Communication with the vehicle control unit (VCU) and monitoring system is performed over a CAN bus interface as shown in figure 11.
Alternatively, the microcontroller can communicate with an external device through a serial RS485 or SPI interface, depending upon the desired final hardware infrastructure. The microcontroller can also concurrently communicate with the Embed GUI through a second serial interface or over the JTAG interface, if additional debugging is required during this procedure.
The firmware as developed in figure 11 can be applied to BEVs, with modules similar to the bq76PL455EVM located near the monitored cells in the battery pack and a single BMS monitoring and control, microcontroller board located in a central and accessible location in the vehicle.
Figure 11: Independent operation of the BMS system with CAN bus communication with the vehicle control unit (VCU), and BMS firmware ready for application with in-vehicle operation.
Conclusions
The examples have been successfully developed with the TI bq76PL455EVM evaluation module equipped with the TI bq76PL455-q1 BMS chip. The BMS algorithms can be completely developed, debugged and verified in the Embed IDE for production-ready applications. The algorithms can be easily developed for (or converted to) other manufacturer’s BMS chips, and their corresponding evaluation modules such as:
- The evaluation module EVAL-L9963 using the ST L9963 chip - https://www.st.com/content/st_com/eval-l9963.html
- The evaluation module TLE9012AQU_DTR_BMS2 using the Infineon TLE9012AQU chip - https://www.infineon.com/cms/en/product/evaluation-boards/tle9012aqu_dtr_bms2/
- The evaluation module FRDM33771BTPLEVB using the NXP MC33771B chip – FRDM33771BTPLEVB | MC33771 TPL EVB | NXP Semiconductors
- The evaluation module DC2259A using the Analog Devices LTC6811 chip – DC2259A Evaluation Board | Analog Devices
- The evaluation module MAX17853EVKIT using the Maxim MAX17853 chip – MAX17853EVKIT Evaluation Kit for the MAX17853 - Maxim Integrated
The communication, control, and monitoring algorithm has been developed for the TI TMS320F28379 microcontroller and can be easily converted for any automotive compatible or other microcontroller such as the TMS570 from TI, the Aurix series from Infineon or any of the STM32 chips.
The development and debugging of the communication, control, and monitoring algorithms was greatly simplified using the visual, model-based development environment of Embed: A complete, production-ready design of the BMS firmware can be developed using only the Altair Embed IDE.
Learn more about Embed through comprehensive help guide : Embed Help
References
- Texas Instruments: SLUUBA7A, bq76PL455EVM and GUI User Guide; https://www.ti.com/lit/ug/sluuba7a/
- Texas Instruments: SLUSC51C, bq76PL455A-Q1 Datasheet; BQ76PL455A-Q1 data sheet, product information and support | TI.com
- Texas Instruments: SLVA617A, bq76PL455EVM Software Design Reference; bq76PL455A-Q1 Software Design Reference (ti.com)
- Electronic Design: Battery Management ICs give Electric Vehicle Batteries a Boost; https://www.electronicdesign.com/power-management/media-gallery/21150953/battery-management-ics-giveelectric-vehicle-batteries-a-boost
About the author
Anthony Boon
He has thirty-five years of experience in the power electronics industry in Australia and Europe, designing, developing and verifying complete power conversion systems, from the power and control electronics, magnetic and thermal design, control algorithms and firmware design. His last 25 years have been especially dedicated to the digital control of those systems for real-time embedded control and simulation of power conversion systems using Altair Embed, which has been a critical tool for his work in this area.
Over the past 20 years, he has been working as a consultant in the fields of power conversion technology and digital control, developing complete systems for customers such as critical battery back-up systems including the development of the appropriate battery management technology.
Comments
-
This is an excellent article, I'm looking forward to trying Altair Embed with the DPD add-on.
2 -
Really nice article. Thank you for taking the time to write this.
0 -
The example diagrams used in this article can be found in the Digital Power Designer add-on to Altair Embed under Examples --> Applications --> Battery Monitoring Systems. There are also examples there for the Infineon TLE9012 BMS evaluation board.
0