3 Lesser-Known Features of Optistruct for Higher Efficiency
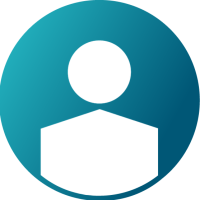
Designing and optimizing a structure or a system can be a challenging task for engineers. We are often faced with the need to design for multiple objectives and criteria, which can be conflicting. In addition, the design space is often very large and complex.
Fortunately, we have tools such as Altair Optistruct that can help us tackle these challenges. However, it is important to use these tools in the right way to get the most out of them. In this article, I will take you through three lesser-known features in Optistruct which are - Defining contact pairs using the "Component Contact" tool, Using RSM to speed up optimization and Customizing "Material Data" with “User-defined Materials”.
I hope that you will find these features useful in your own work! So, let’s get started.
1. Defining Contact Pairs:
One way to use Altair Optistruct more effectively is to take advantage of the "Component Contact" tool. This tool allows you to define contact pairs between different components in your model. This can be useful for analyzing assemblies and simulating real-world contact conditions. To use this tool, you first need to select the "Component Contact" tool from the "Tools" menu. Then, you need to select the components that you want to include in the contact pair. Finally, you need to specify the contact type, such as bonded, frictional, or sliding.
For example, if you want to simulate a perfectly bonded joint where the bolt and plate are stuck together, you can choose the bonded contact type. If you want to simulate a joint with some friction between the bolt and plate, you can choose the frictional contact type.
2. The Optimization Response Surface feature:
This feature allows you to use response surface methodology (RSM) to speed up optimization. This involves building a surrogate model of the objective function, which can be used to quickly evaluate different design alternatives. To use this feature, you first need to specify the design variables, objective function, and constraints. Then, you need to select the "Optimization Response Surface" tool from the "Tools" menu. Finally, you need to select the "Build Response Surface" option.
For example, you can use this feature to evaluate the optimal design of the cantilever beam for different values of the design variables, such as the beam's width, height, and length. You can also evaluate the impact of changing the constraint on maximum stress on the optimal design. This can help you to find the best design for the cantilever beam quickly and efficiently.
3. Customizing Material Data:
One of the least-known but important features of Optistruct is the ability to customize material data. This can be done using the "User Defined Materials" feature, which enables you to define material properties such as density, Young's modulus, Poisson's ratio, and thermal conductivity. This can be useful for simulating materials that are not available in the standard material libraries.
Let's say you want to simulate the behavior of a composite material that is not available in the standard material libraries of Optistruct. The composite material consists of carbon fiber reinforced polymer (CFRP) and has different material properties than the standard materials available in Optistruct.
To use the "User Defined Materials" feature, you would first define the material properties of the composite material, such as density, Young's modulus, Poisson's ratio, and thermal conductivity. You can obtain these material properties from experimental data or from published literature on CFRP materials. Next, you can use Optistruct's "User Defined Materials" feature to create a custom material entry for the composite material. This allows you to specify the material properties that you have defined for the composite material.
To sum it up, using the advanced features and techniques discussed in this article, engineers can gain a deeper understanding of how their designs will behave under different conditions and make informed decisions to improve their designs.
I encourage you to try out these features and share your feedback.