Modeling Particles in Flow
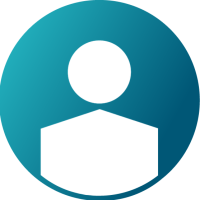
Modeling Particles in Flow with Altair Products
The Altair tool suite provides a variety of ways to model particles in flow which are applicable to many use cases across a wide range of industries including Agriculture, Pharmaceutical, Mining, and Material Processing. Based on the number and relative size of the particles, the solid volume fraction, how particles interact with each other, and how the user would like to track the motion of the particles Altair AcuSolve and Altair EDEM provide appropriate highly accurate solutions in a short amount of time.
Options
AcuTrace
Compute the evolution of massless particles or particles with mass through a steady or transient flow field. Particles can be tracked through interface surfaces, moving mesh regions, or reference frame regions. AcuTrace can be run in a sequential or coupled manner with AcuSolve. Heat transfer between particles and the fluid can be calculated. Particles can collide with walls and exit the domain, but particles do not collide with each other. Breakup, coalescence, and accumulation of particles is not permitted. AcuTrace is a separate executable from AcuSolve and establishes a socket connection when running coupled.
Euler-Euler Multiphase
As the most comprehensive model for multiphase flows, the Eulerian-Eulerian multiphase feature provides more fidelity and accuracy than other disperse multiphase methods. This feature allows users to model dispersed particles within a carrier fluid. Particles can be flecks of dust or powder (solid), droplets of water (liquid), or bubbles (gas). Tracking of particle phases is modeled by the full exchange of momentum between dispersed fields and the carrier phase. Mass and momentum are conserved for each phase. Particles are not individually tracked, rather, ensemble-averaged values are modeled within an Eulerian frame of reference. Fluid particles can accumulate to eventually form a continuous medium. As multiphase flows are inherently transient the solver is run transient. However, solid particle interaction is ignored. Boundary conditions for particle flow can be steady or time varying. Heat transfer and boiling is permitted with Eulerian-Eulerian multiphase.
Granular Multiphase
As an extension to the Eulerian-Eulerian multiphase feature, Granular multiphase additionally accounts for the behavior of solid phases. When the volume fraction of solid particles becomes high, roughly in the range of 20% -- 60%, the solid pressure and solid viscosity effect of accumulated solid media becomes important to correctly characterize the flow. Other parameters related to solid particle motion and their behavior in densely packed conditions are also available. Particles are not individually tracked, rather, ensemble-averaged values are modeled within an Eulerian frame of reference. As multiphase flows are inherently transient the solver is run transient. Boundary conditions for particle flow can be steady or time varying. Heat transfer is permitted with Granular multiphase.
AcuSolve/EDEM Coupling: Sequential Steady
When more fidelity is needed regarding particle-particle interaction in a dominant carrier flow, the Sequential Steady approach with AcuSolve and EDEM is the most appropriate. In this process, the flow field is solved to a steady state with AcuSolve and imported into EDEM. Particles will react to the presence of the carrier fluid due to hydrodynamic forces while particle-particle and particle-wall interactions are also supported. Heat transfer from the fluid to the solid particles is permitted but particle temperatures will not be realized in the flow field. Particle accumulation will not alter the flow field with this approach. As this approach is best suited for dispersed particles, the solid volume fraction should be less than 5%.
AcuSolve/EDEM Coupling: Sequential Transient
When more fidelity is needed regarding particle-particle interaction in a transient carrier flow the Sequential Transient approach with AcuSolve and EDEM is the most appropriate. In this process AcuSolve calculates the flow field and EDEM calculates the particle motion uni-directionally but in a sequential manner. The flow field from AcuSolve is continuously updated on the EDEM side and the particles react to changes in the flow field. However, any distribution or accumulation of particles on the EDEM side is not communicated back to AcuSolve. This approach is useful when model component motion is required or when boundary conditions are changing in time. Heat transfer from the fluid to the solid particles is permitted but particle temperatures will not be realized in the flow field. As this approach is best suited for dispersed particles, the solid volume fraction should be less than 5%.
AcuSolve/EDEM Coupling: Coupled Transient
For maximum physical accuracy of particles within a flow field, Altair HyperWorks offers the AcuSolve/EDEM Coupled Transient approach. In this process AcuSolve calculates the flow field and EDEM calculates the particle motion sequentially while coupling forces are shared between two solvers bi-directionally. Particle accumulation is permitted and can alter the flow field. The presence of particles is communicated to AcuSolve from EDEM via a volume fraction representation in the flow. Particles interact with one another, with stationary and moving walls, and with changes to flow or thermal boundary conditions. Bi-directional heat transfer is supported with this approach. A common use case for this approach is the fluidized bed case.
EDEM only: No co-sim
There are a wide variety of use cases where the motion of particles and their impact on or from the surrounding air is inconsequential. For these cases no co-simulation with AcuSolve is necessary. EDEM without co-simulation simulates the motion of particles, their interactions with each other, interactions with stationary or moving walls, steady or transient boundary conditions, accumulation, heat transfer, and particle coalescence or breakup.
Summary
Modeling Particles in Flow with AcuSolve
Simulating particles in flow with Altair tools can be done quickly and accurately using one of the many methods mentioned above. Users should first determine to what extent the fluid flow will impact the motion of the particles or vice versa. If no significant interaction is expected EDEM should be considered without co-simulation. If the particle distribution is expected to be dense or if dense accumulation of particles is something the user would like to capture physically, two options are available based on whether individual particles must be tracked. AcuSolve/EDEM Coupled Transient should be used to track individual particles and AcuSolve Granular Multiphase should be used if ensemble averaging of the particle cloud is appropriate or sufficient. If the particle distribution is assumed to be dilute or disperse users should decide if modeling particle-particle interaction is required. If particle-particle interaction is not expected or necessary to calculate then the question of tracking individual particles should be answered. If tracking individual particles is important then AcuTrace should be considered. AcuTrace can be run sequentially or coupled with AcuSolve. If tracking particles individually is not possible or not desired, then AcuSolve’s Eulerian-Eulerian multiphase capability should be considered. For dilute flows where individual particle tracking is desired either the AcuSolve/EDEM Sequential Steady or Sequential Transient approach will be best, depending on the transient nature of the setup or solution. Coupled simulations will generally require longer simulation times than single solver runs but the added calculations provide more fidelity to the final solution. See below for a decision tree of the above as well as a summary table of the various features.
- Available in EDEM solution only
- Heat transfer is from fluid to particles only