Optimizing Washing Machine Control with Power Electronics and Multi-Body Dynamics Integration
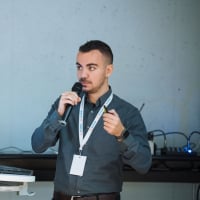

Holistic System Level Approach
We've all experienced a washing machine vibrating, sometimes even "walking" across the floor as if it was a living thing. In this blog, we'll explore how you can identify and possibly mitigate these annoying vibrations when designing such systems with Altair tools.
[click play to watch]
This short video is a product of a system level simulation that combines power stage and control (rectifier, inverter, PMSM, and control) with the multibody dynamics of the washing machine drum and dampers.
Simulating electrical motor drives at the full system level— e-power stage plus the mechanical load — is usually complex. Firstly, integrating the electronics along with the mech system can be slow due to the different time constants involved. What is more, different engineering teams often use various simulation tools that don’t integrate well, making a unified approach challenging.
Altair begs to differ by providing all the "puzzle" pieces needed for a complete motor drive system simulation:
1. E-power Stage/Power Electronics: Altair PSIM with ability to include a PMSM motor designed in Altair Flux
2. Multibody dynamics/Complex Mech loads: Altair MotionSolve
3. System-Level Integration: Altair Twin Activate, allows for easy co-simulation of PSIM, Flux, and MotionSolve.
All of this without breaking the bank, thanks to the Altair Units licensing system. In fact, this is where Altair's cost-effective and efficient licensing model shines.
Let's explore each piece separately.
PSIM
Altair's specialized solution for power electronics. The speed of PSIM when it comes to switching simulations is unparalleled. Speed and robustness are critical factors that enabled this complex workflow, after all.
Many engineering teams avoid switching simulations at the system level for motor drives. This is to be expected when dealing with simulations tools that do not provide the right fidelity-to-speed ratio to make the effort worth it. Instead, they rely on exchanging data between control/system teams and motor design teams using lookup tables and scripting. This approach often leads to inefficiencies and disjointed workflows.
Altair’s PSIM and Flux integration provides a smarter alternative. It leverages PSIM's speed for inverter simulations while allowing users to continue their lookup table approach for the motor within a unified, user-friendly environment—eliminating the need to script every step.
You can find more details on how this connection works and what is the added value here:
Flux-PSIM Coupling : Leverage the system simulation speed while working around your Motor Design
The lookup table approach extends beyond just the motor model from Flux. To enhance the fidelity-to-speed ratio—since that's what ultimately matters—we also provide lookup table models to calculate switch thermal losses and battery dynamics. PSIM offers various fidelity options, and if you need fast calculations for system-level control decisions or thermal losses, this capability will be particularly valuable.
Fidelity-to-speed ratio is what makes our approach stand out.
While we won't dive into specific motor drive and control design techniques like FOC or FW, the bigger picture is clear:
This entire simulation can be developed collaboratively between the system/inverter/control teams and the e-motor teams when a Flux motor model is involved.
Especially for the mechanical engineers in the thermal, motor, and MBD teams, the goal is to treat all the 'electrical stuff' as a 'black box' from their perspective. This is exactly how we approach it using the PSIM-Twin Activate co-simulation capability.
The environment shown above is Twin Activate, where the entire PSIM motor drive simulation is encapsulated into a PSIM co-simulation block. We’ll discuss Twin Activate in more detail later.
The inputs are the target speed and motor speed feedback from the mechanical load. The output, the motor's torque, feeds into the mechanical load simulation (MotionSolve). This closes the loop: PSIM generates torque, which sets the motor speed in MotionSolve, and this speed is used for control setup and to drive the load in PSIM.
For more insights into how the load is set up in PSIM, refer to the first picture above. This blog may get lengthy if we delve into detailed analysis, so feel free to reach out to Altair Support for further information or assistance with similar implementations.
MotionSolve/MotionView
Altair's multibody simulation solution lets you create and analyze complex mechanical systems to assess dynamic responses. Engineers can graphically construct models with realistic geometry, loading conditions, flexibility, damping, friction, and multiphysics effects.
In this case, it was used to design a high-fidelity MBD load to be coupled with the motor drive shaft from PSIM.
The CAD file of the washing machine is imported and the moving parts, along with dampers, are defined:
In this case, the clothes are modeled as a single rotary object with either a 5 kg concentrated mass or a fixed 0.5 kg mass to simulate eccentricity. While Altair's EDEM tool can model fabric as discrete elements, adding significant complexity and potentially impacting simulation speed, it was omitted for this demonstration.
MotionSolve co-simulates with Twin Activate, where motor torque coming from PSIM serves as input and the MBD model provides feedback data for speed and bin vibrations.:
Again, the environment shown is Twin Activate, where the entire MotionSolve simulation is encapsulated into the MotionSolve co-simulation block.
Twin Activate
This is where everything comes together. Twin Activate is a flexible integration solution that supports even non-Altair model formats like FMI/FMU and reduced-order models using machine learning techniques such as romAI for dynamic fitting.
An interesting example of romAI in power electronics and motor drives can be found here:
Sensorless Control of Permanent Magnet Synchronous Motors (PMSM) powered by ROM and Machine Learning
Back to the washing machine example, PSIM and MotionSolve co-simulation blocks can be connected in this manner, while allowing multidisciplinary teams to remain focused on their individual stages. This setup provides a shared platform for testing system-level interactions, which is crucial, as we will see later.
To summarize:
1. The motor drive, consisting of a permanent magnet synchronous motor (PMSM) and its controls, is modeled in PSIM. The overall system behavior is influenced by the control bandwidth, decided in PSIM.
2. A high-fidelity model of the mechanical subsystem is created in MotionView and analyzed with MotionSolve to assess dynamics and vibrations based on drum speed and clothes weight.
3. Twin Activate serves as the integration platform, enabling comprehensive evaluation and optimization of the entire system, including feedback between mechanical effects and motor control.
Let’s review some key results and steps of the workflow, demonstrating the value of different fidelity modeling. These insights will be highlighted in the slides below:
- Dynamics and Vibrations: Modeling the washing machine’s dynamics and vibrations based on holistic system approach.
- Observations: Vibrations in MotionView are influenced by control choices and dampers.
- Torque Analysis: High-fidelity torque and current waveforms are evaluated, incorporating feedback from the mechanical model in MotionView.
- Control Design: Designing control bandwidth with a realistic closed-loop system can save testing time.
Refer to the slides below to see the added value of the PSIM + MotionSolve connection compared to a simplified average controller model.
The simulation files can be found attached. You can directly open the "washing_machine_w_PSIM_MS.scm" that will include the PSIM and MS co-simulation blocks. Please make sure that the MS paths in Twin Activate (File >> Preferences >> Paths) are correct before running the simulation.
Next Steps
It's not over yet! There is one more trick in our sleeves. Using fit models for the entire motor drive system, as showcased here:
It’s not over yet! We have one more trick up our sleeve. Using fit models for the entire motor drive system, as demonstrated here:
[Fit model of an entire motor drive]
This approach significantly speeds up simulations while maintaining high fidelity. By leveraging PSIM simulation data to train a static fit model with HyperStudy, you can achieve efficient and accurate results.
Forget guesswork and rough estimates! You can now integrate high-fidelity data into your system-level simulations derived from advanced data analytics algorithms.
We’re continuously advancing in this area, so stay tuned. This represents a major leap in power electronics simulation, bridging data analytics with machine learning techniques.
Helpful Links
- AC Sweeps with PSIM: What makes them unique?
- PSIM & Flux Connection : Leverage the system simulation speed while working around your Motor Design
- PSIM & Twin Activate connection tutorial
- PSIM & Flux & MotionSolve - Electric Motorcycle example
- Modelling a Bulk Solids Mixer Drivetrain with EDEM, MotionSolve, PSIM and Activate example
- PSIM & HyperStudy connection tutorial
- Insights into Motor Drive Design: Analyzing Trends and Long-Term Costs with PSIM and HyperStudy
- Combining Multiphysics Simulation and Automated Design Exploration to Optimize Performance and Cost of your Motor Drives