The hard thing about EMI compliance in power converter design
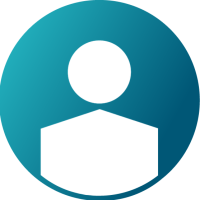

Power converters can generate electromagnetic noise in electric systems that will be conducted through the wires and may disturb the operation of other components that are connected to them. These ElectroMagnetic Interference (EMI) issues must be considered as all products need to meet noise thresholds defined by the relevant standard. The constant search for higher efficiencies and converter compactness leads to use higher switching speeds. Because of parasitic inductances and capacitances in the circuits, the faster device transitions also increase electromagnetic noise.
Typical EMI signal output compared to standard requirements
Altair PSIM is a simulation tool that can be used to drive conducted EMI design decisions during the initial stages of power converter design. Instead of playing guess and test during testing in the chamber. There are several key design decisions that can impact what the conducted EMI performance will be. The most important is the selection of the active switches and how they are gated & snubbered. In effect you are trading losses in your active switches vs EMI filter requirements and losses in the EMI filter, what is the optimal scenario? There are also several other design decisions that can be made to optimize cost and parts, but will have a hidden impact on EMI.
Typical workflows for considering conducted EMI can struggle with all but the simplest topologies and simulation times can easily exceed 60 minutes. This is due to small L and C values that will introduce difficult time constants for circuit simulators. PSIM’s robust solver combined with advanced non-ideal models for the switches enable PSIM to deal with those stiff equations and reach convergence in reasonable times, where other solvers will be slow or will just stop. Parallel simulations can also be run through automated design exploration using a set of initial conditions as starting points. This unique workflow will increase simulation throughput of test scenarios by an order of magnitude vs other methods. These workflows will also work on complex and non-trivial systems, for example to look at the impact of changing from a 2-level inverter to a 3-level t-type.
Motor drive model in PSIM taking into account parasitics introduced by long cables.
Conducted EMI issues are often detected very (too) late in the design process, when measuring on prototypes. This usually leads to costly iterations that you want to avoid. Let’s address these upfront and not leave it as an afterthought. Simulation can help system engineers gain a better insight of the subsystem operations from EMI perspective and derive detailed hardware/mechanical layout specifications. It can also help hardware engineers to carry out hardware component selection and EMI filter design to meet the EMI requirements before the actual circuit boards/system layout starts.
Want to learn more? Please join our webinar series on power electronics: Register Here
Albert Dunford & Vincent Leconte