Contact vs Equivalence
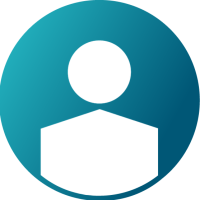
I'm simulating a shaft, subjected to vertical and horizontal forces, as well as a torque. The shaft consists of a pipe with an internal disc that is welded from the outside of the pipe.
I've modeled the connection between the disc and the internal face of the pipe once as a "Freeze" connection, and once as equivalenced nodes of the disc and the pipe. The stress results for both simulations are different. Why is that?
Note: I did have to refine the mesh in the disc in order to equivalence the nodes
Which model is more appropriate for this type of connection (the disc serves as a backing for a full penetration groove weld of two pipe segments)?
Freeze contact results:
Equivalent nodes results:
Answers
-
peak stresses at the freeze contact area is expected to be discontinuous. So usually it is better to use a matching mesh in this case.
But if you compare far from the interface, results should match quite well. (your images have different legend values, so it is hard to compare.
But bringing them to the same legend values, they should match ok except for the elements imediately in the contact region.
2 -
Adriano A. Koga_21884 said:
peak stresses at the freeze contact area is expected to be discontinuous. So usually it is better to use a matching mesh in this case.
But if you compare far from the interface, results should match quite well. (your images have different legend values, so it is hard to compare.
But bringing them to the same legend values, they should match ok except for the elements imediately in the contact region.
I realized that comparing the coarse mesh with a freeze contact to a fine mesh with equivalenced nodes is not a good comparison. So I detached the equivalenced nodes and reran the model with a freeze contact.
The results now match very well:
What I still don't understand is why refining the mesh on the disc affected the max stress in the tube via the freeze contact.
0