Pin Bearing Test
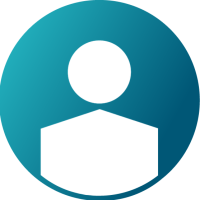
Hi, i'm trying to simulate a pin bearing test on a composite material. The idea is to force the pin to translate along the x axis with a constant velocity of 3mm/min and in this way the pin should create a damage in the composite part. In my model I used constant displacement instead of velocity but i think it is the same. My problem deals with the contact edges between the hole and the pin. Infact, when i run the simulation there is no error in the solver, but looking at the post processing in hypermesh in displacement section the only things that it moves is the pin without making any damage in the composite part. I share the model to better understand the problem.
Thank you in advance, i would appreciate if could help me.
Answers
-
contacts are usually surface to surface or node to surface.
Your contact region is edge to edge. For freeze (glued) contact this would be ok.
I suggest you to create a solid cylinder for your pin, and build a contact surface on the solid surface, and use it as the master surface of your contact.
Your slave in the contact would be a set of nodes of the edge of the model (Node2Surface). Usually it would be better to have the slave set more refined than the master surface.
another simplified way of modeling your contact it to use CGAP elements between your nodes/edges.
CGAP elements use PGAP properties and you can define different stiffeness under compression and traction (KA and KB) and the limit displacement U0, whre the stiffness change. Take a look at the Help for OptiStruct PGAP for more details.
0 -
I really appreciated the advice. I created the solid pin, the contact surface on it and i selected N2S. Unfortunately i haven't been able to test the solution because once i try to create the spcd constrain the solver blocks and tells me that there is ERROR 186 even if there is the spc constrain in the same node. I can't fix it. I also tried to use a cylindrical surface as a pin to semplify the problem due to the fact that the pin could be considered non-deformable in this test but i had the same error.
In attachment there are the two versions of the problem, than you in advance for your help.
0 -
Giacomo Ranzini said:
I really appreciated the advice. I created the solid pin, the contact surface on it and i selected N2S. Unfortunately i haven't been able to test the solution because once i try to create the spcd constrain the solver blocks and tells me that there is ERROR 186 even if there is the spc constrain in the same node. I can't fix it. I also tried to use a cylindrical surface as a pin to semplify the problem due to the fact that the pin could be considered non-deformable in this test but i had the same error.
In attachment there are the two versions of the problem, than you in advance for your help.
Before going to your question:
For composites you NEED to check material orientation (2D>composites>material orientation), otherwise your fibers will be pointing totally wrong.
Another thing to check is balancing and symmetry, as warping might occur.
Now, considering your model:
you have created a 'linear transient' analysis.
Actually, as it involves contacts your should use the NL Static loadcase.
For this, you need load collectors NLPARM and NLOUT, and create a NLSTAT loadstep.
inside your loadstep, you will associate the NLPARM(LGDISP) and the NLOUT.
For this case, you don't need TLOAD, nor SPCD.
Just create a SPC in your pin, will all DOFs zero, except the one you want moving, in this case, in X direction with value 9.0. (nonlinear incremental analysis will increase from 0.0 to 9.0 in the end)
For convergence purposes, i would recommend using a larget number of increments NT in you NLPARM. (i.e: 1000) as you want a small initial increment to settle down the contacts initially.
Make sure also your contact is using FINITE or CONSLI options.
For nonlinear, take care with your 'pin' thickness, as you might create interference with your plate.
As you have a rigid in the middle, you can define a thickness really low, usch as 0.001. Otherwise, the contacts will try to push the interference away, causing really high strains.
0 -
Hi Adriano,
thank you for all the priceless advices. I followed all your instructions except for NI value equals to 10 to make the simulation faster and because with NI equals to 1000 i had hardware problems. Unfortunately, I haven't been able to test them because the simulation it is suddently aborted due to ERROR "#4965 maximum time of cutbacks reached". I tried many times to change some parameters but this error still occurred. However, the mesh is still not perfect but i'll fix it once the model works.
I share the model and i would like to thank you so much for the support.
0 -
Giacomo Ranzini said:
Hi Adriano,
thank you for all the priceless advices. I followed all your instructions except for NI value equals to 10 to make the simulation faster and because with NI equals to 1000 i had hardware problems. Unfortunately, I haven't been able to test them because the simulation it is suddently aborted due to ERROR "#4965 maximum time of cutbacks reached". I tried many times to change some parameters but this error still occurred. However, the mesh is still not perfect but i'll fix it once the model works.
I share the model and i would like to thank you so much for the support.
from my tests, the edge of your hole was deforming out of plane, thus creating some hard time for convergence.
0