Tensile test
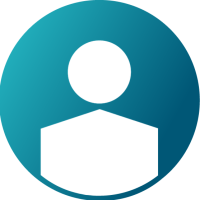
Hi everyone,
I tried to run the tensile test using Radioss. I followed the method and setting from the tutorial file (RD-T: 3500 Tensile Test Setup).
1. When dealing with the flat specimen (as in the tutorial), the analysis gives a good result.
2. I tried to use the round specimen (change the property to P14_SOLID card image). however, the result shows that the specimen does not break. It continues to stretch until the final time. Based on the force versus time graph, the specimen already breaks at T20.
Really appreciate help from other users regarding this problem.
Thank you.
Attached is the image of the result.
Image1= flat specimen
Image2= round specimen T40
Image3= Force vs time
Image4=round specimen T20
Image5= round specimen T20.5
Answers
-
Hi,
I'm not a Radioss expert, but the graph shows that your specimen loses stiffness at T20, and not exactly breaks.
Depending on your material settings and configuration, when your element (integration points) reaches a certain strain, your material will feel a drop in stiffness, and potentially be deleted from your analysis.
For deletion I believe you need to add a failure parameter into your material constants or assign a failure model to your model. Then, depending on the strains, you will see your part breaking, due to element deletion.
0 -
Adriano A. Koga_21884 said:
Hi,
I'm not a Radioss expert, but the graph shows that your specimen loses stiffness at T20, and not exactly breaks.
Depending on your material settings and configuration, when your element (integration points) reaches a certain strain, your material will feel a drop in stiffness, and potentially be deleted from your analysis.
For deletion I believe you need to add a failure parameter into your material constants or assign a failure model to your model. Then, depending on the strains, you will see your part breaking, due to element deletion.
Hi Adriano,
Thank you for the reply. I already add the failure parameter in the material properties (Johnson cook), but the problem is still there.
Is the failure parameter is constant for the flat and round specimen? As you can see in images 1 and image 2, I am using the same material for flat and round. The flat specimen shows it breaks while the round specimen only stretches.
If you have other solution and suggestion on this matter, please share with me.
Thank you.
0 -
Hi,
The built-in failure criteria from LAW2 deletes only shell elements. From the Help page:
For solid elements you will need a failure criteria property associated to the LAW2. Add a /FAIL/JOHNSON for example, with a D1 value equal to the failure plastic strain.
1 -
Rodrigo Merigo_22161 said:
Hi,
The built-in failure criteria from LAW2 deletes only shell elements. From the Help page:
For solid elements you will need a failure criteria property associated to the LAW2. Add a /FAIL/JOHNSON for example, with a D1 value equal to the failure plastic strain.
Hi Rodrigo,
Thank you for the solution. Here is the input parameter for the material. Kindly suggest the important input required by the material. Is my material input correct?
I just add the failure model to the file. will update here the result later.
Thank you.
0 -
Hi,
Dimensionally, it looks correct. You can get more details in the corresponding pages of the help:
0 -
Rodrigo Merigo_22161 said:
Hi,
Dimensionally, it looks correct. You can get more details in the corresponding pages of the help:
Hi,
Thank you for the reference documents. Here is the plot for the stress strain.
Is normal to have fluctuation data at the end of the curve? Is there any problem with the result? I tried to extract data from the plot.
Here are some of the results.
E = 140 GPa
Yield stress = 0.474 GPa
Ultimate tensile stress = 0.74253 GPa
Failure plastic strain = 0.149
The result shows lower E and failure plastic strain values than the input data in the material. Is there any solution for this matter? Appreciate your help.
0