Essential Steps To Start With Nonlinear FEA
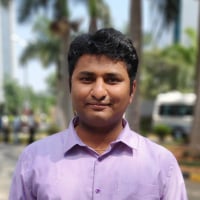
Rahul_P1
Altair Employee

Essential Steps To Start With Nonlinear FEA
• Learn first how the software works on a simple model before you use a nonlinear feature which you haven’t used. Also guess
how your structural component will behave, i.e. check for available studies, reports and benchmarks .
• Try to understand the software’s supporting documentation, its output and warnings.
• Know what you are looking for. Prepare a list of questions you think your analysis should be able to answer. Design the
analysis, including the model, material model, and boundary conditions, in order to answer the questions you have in mind.
• Keep the final model as simple as possible. A linear analysis done first can provide a lot of information such as where are
the high stresses in the model, where the initial contact may occur, and what level of load will introduce plasticity in the
model. The results of the linear analysis may even point out that there is no need for a nonlinear analysis. Examples of such
a situation include the yield limit not being reached, there is no contact, and the displacements are small.
• Verify and validate the results of the nonlinear FEA solution. Verification means that “the model is computed correctly” from the
numerical point of view. Wrong discretization with respect to the mesh size and time stepping are common errors. Validation
asks the questions if “the correct model” is computed e.g. the geometry, material, boundary conditions, interactions etc
coincide with the one acting in reality.
• Try to look into the assumptions made with respect to the structural component, its geometry behavior with respect to large
strain (On/Off), look into different material models if the earlier model is unable to give you a result you expect (sometimes
software only make some models compatible with commonly used elements and in this case you might look into a possibility
of changing the element formulation).
Tagged:
0
Answers
-
Essential Steps To Start With Nonlinear FEA
• Learn first how the software works on a simple model before you use a nonlinear feature which you haven’t used. Also guesshow your structural component will behave, i.e. check for available studies, reports and benchmarks .• Try to understand the software’s supporting documentation, its output and warnings.• Know what you are looking for. Prepare a list of questions you think your analysis should be able to answer. Design theanalysis, including the model, material model, and boundary conditions, in order to answer the questions you have in mind.• Keep the final model as simple as possible. A linear analysis done first can provide a lot of information such as where arethe high stresses in the model, where the initial contact may occur, and what level of load will introduce plasticity in themodel. The results of the linear analysis may even point out that there is no need for a nonlinear analysis. Examples of sucha situation include the yield limit not being reached, there is no contact, and the displacements are small.• Verify and validate the results of the nonlinear FEA solution. Verification means that “the model is computed correctly” from thenumerical point of view. Wrong discretization with respect to the mesh size and time stepping are common errors. Validationasks the questions if “the correct model” is computed e.g. the geometry, material, boundary conditions, interactions etccoincide with the one acting in reality.• Try to look into the assumptions made with respect to the structural component, its geometry behavior with respect to largestrain (On/Off), look into different material models if the earlier model is unable to give you a result you expect (sometimessoftware only make some models compatible with commonly used elements and in this case you might look into a possibilityof changing the element formulation).0