PCOMP and PCOMPG
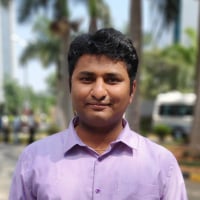

I am interested to know if there is any difference in the way elements with PCOMP, PCOMP and PCOMPG cards are calculated. Or if it is only for preprocessing or graphical purposes.
In particular, I would like to know if the interfaces (e.g. T connections) defined with PCOMG account in any way for the real “path” of the ply (thus introducing extra stress concentrations).
Thanks
Answers
-
-
PCOMPG considers the PLY runout through the thickness variations based on global ply IDs. PCOMPG comes handy when there is a change in thickness/cross section or drop number of plies from one end to other.
whereas PCOMP doesn't consider these changes. It just takes the PLIES and aligns according to what you give. its useful when the cross section/thickness is uniform through out the model.
0 -
I have modeled a simple structure with four plies (refer to the first picture from bottom layer 90,45,-45,0) with both PCOMP and PCOMP(G).
Check the results for composite stresses for PCOMPG (left) and PCOMP (right)for 3rd ply.
the stresses in 3rd ply on PCOMPG is less compared to PCOMP, because PCOMPG maintains the associativity among the plies based on Global PLY number where as PCOMP doesn't.
0