Drop Test- Sudden Increase in Internal Energy and Kinetic Energy - RADIOSS
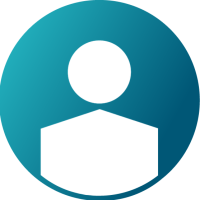
I am doing drop test in RADIOSS.
The simulation initially runs fine, but suddenly at 0.48ms, internal energy, kinetic energy and rotational kinetic energy goes to e^200. What could be the possible reason for it and how to rectify it?
Thank You.
P.S: I have attached the .out file.
Answers
-
Your Part 23 has huge KE and IE at that point and node 990646 is controlling the timestep, so look in those locations first, it might be contact related?
Something you can try? since you know it falls over at cycle 38031:
It may be useful to help debug, to set the termination time in your 0001.rad at .4818e-3, then duplicate your 0001.rad to a 0002.rad that is the same as your 0001.rad, but with an animation output frequency of 1e-8 (you should get an animation file almost every cycle at the end then and should be able to 'see' where the problem is occurring)
0 -
Paul Sharp_21301 said:
Your Part 23 has huge KE and IE at that point and node 990646 is controlling the timestep, so look in those locations first, it might be contact related?
Something you can try? since you know it falls over at cycle 38031:
It may be useful to help debug, to set the termination time in your 0001.rad at .4818e-3, then duplicate your 0001.rad to a 0002.rad that is the same as your 0001.rad, but with an animation output frequency of 1e-8 (you should get an animation file almost every cycle at the end then and should be able to 'see' where the problem is occurring)
Hi Paul,
In the animation it is showing that at node 990646, one element is getting stretched.
How can this be avoided?
I have attached the images, and the property, contact and material card image. Please have a look at them.
0 -
Props and Mat and Contacts look ok overall, your material is very soft though? (Modulus of only 192MPa?)
Maybe you need some failure or plasticity?
Is this in an area of contact? Or does that node just pop out, You could try removing the STMIN value and see if that helps
Paul
0 -
Paul Sharp_21301 said:
Props and Mat and Contacts look ok overall, your material is very soft though? (Modulus of only 192MPa?)
Maybe you need some failure or plasticity?
Is this in an area of contact? Or does that node just pop out, You could try removing the STMIN value and see if that helps
Paul
Yes, that node is in area of contact. I will remove STMIN and check.
Also, at the corner, some elements are self penetrating. At present, I have used TYPE24 to give self-contact. But this isn't working.
How to avoid this self-penetration?
0 -
Neeraj Kumar said:
Yes, that node is in area of contact. I will remove STMIN and check.
Also, at the corner, some elements are self penetrating. At present, I have used TYPE24 to give self-contact. But this isn't working.
How to avoid this self-penetration?
You mean they are becoming negative volume? Due to compression? Then again, I would suggest adding a failure criteria to erode the elements before this rather than an elastic material.
If you want to create a self contact internally on the part, you can use Type 7 interface and /SURF/PART/ALL for the group type for the main surface (and all nodes for secondary node set).
0 -
Paul Sharp_21301 said:
You mean they are becoming negative volume? Due to compression? Then again, I would suggest adding a failure criteria to erode the elements before this rather than an elastic material.
If you want to create a self contact internally on the part, you can use Type 7 interface and /SURF/PART/ALL for the group type for the main surface (and all nodes for secondary node set).
Hi Paul,
TYPE7 is to give self-contact for shell mesh? How to provide self-contact for solid mesh part?
0 -
What I described was for Solid!, if you use a surf of type /SURF/PART/ALL for the main side of the contact (your part) it considers all internal facets of the solid and then you can use a GRNOD of all the nodes of the part as the secondary, set gapmin to some relevant value, e.g. if your elements are 3mm, set it to 0.3mm to stop them compressing more than around 90%
0