Composite Optimization
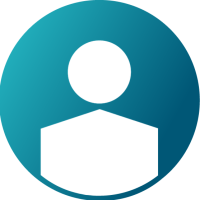
Hello everyone, I'm trying to optimize a composite component (which is freezed together with some aluminum components) that has already been modeled and analyzed in Hypermesh using a plybook with 86 plies.
Some Information to my setup:
Plies: 0° : unidirectional carbon fiber 0.1mm ----- 45°, 90°: carbon fiber fabric 0.2mm
I have created two material cards and defined a property card as PCOMPP and entered the data of those that they have been laminated together (Z0 Option: Z0=0, Laminate option: total). After some research, I found out that I should change the laminate setting to smear before optimizing it and I changed it.
Goals:
I want to keep the mass as low as possible and at the same time reduce the displacement at a desired point so that the component no longer fails (TSAI WU failure criteria) in a load case. I tried a few things but I was not happy with the results of the FreeSize optimization and I received many error messages during these attempts.
My questions & doubts:
1. I am using the same laminate which I created for the linear static analysis: Should I create a simple layer structure and do the optimizations for it?
2. I have not assigned any material for the composite component because the two materials are defined in the laminate anyway. Am I right?
3. I would like to keep the thickness of the layers the same (0 ° = 0.1mm, 45 ° / 90 ° = 0.2mm) because I only have these materials available. : I've defined 3 Plyman parameters for this... Does anyone have a different opinion?
4. Response: res_mass, res_displacement --> cont_displacement: upper bound has been defined --> objective: min - mass
5. Mindim: Min Member Size > 4 x mesh size but I still get very strange shapes
6. My next steps are size and shuffling optimizations. I also tried to finish the size optimization and before that I updated the TMANUK of all plies and the upper / lower bounds of the design variables... the thicknesses of plies are changing to the desired values but I can not improve the mass or the displacement or the shapes of plies.
7. What would you have done differently than I did? or can anyone identify my mistakes?
I would be very happy for your help or tips.
Best regards
Find more posts tagged with
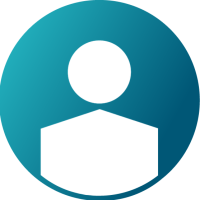
1. Same as analysis
2. Only need material in the ply
3. Plyman, correct.
Hello Adriano, I have received many error messages so far and all the errors have been resolved by doing some research in the forum, but now I am getting the error message: 'INTERNAL PROGRAMMING ERROR # 8011' and I cannot find any information for this.
Can you tell me how I can fix this error?
I have two different versions of hyperworks and I tried both of them: 2019.1 and 2020
Thanks in advance.
Best regards,
Oguzhan
1. Same as analysis
2. Only need material in the ply
3. Plyman, correct.