1 to 1 rigids can be defined between two plates including bolted connection or not?
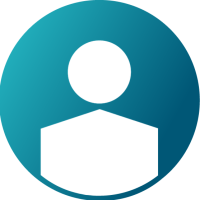
Two plates are connected with bolt. I have modelled two plates with shell mesh and connected with 1d rigid at bolt location and i have given 1 to 1 rigids between two plates and assumed as contact. with this the stresses are reduced comparing with single rigid connection(bolted connection).
Please clarify that my assumption is correct or not?
Answers
-
you could use Contacts in your model, between your plates, instead of creating each single node-node connection.
In CAE there are a lot of hypothesis and assumptions that really depends on what you need to calculate.
0 -
Adriano A. Koga_21884 said:
you could use Contacts in your model, between your plates, instead of creating each single node-node connection.
In CAE there are a lot of hypothesis and assumptions that really depends on what you need to calculate.
Thanks for your reply.
Defining of contacts between two plates is correct? If it is what type of contacts need to be defined?
0 -
Mintu said:
Thanks for your reply.
Defining of contacts between two plates is correct? If it is what type of contacts need to be defined?
hi @Mintu
this is not a simple question to answer, withouth knowing what you're aiming to calculate in your simulation and what is indeed being simulated.
Contacts in general are closer to real life than rigids. But contacts can be:
- linear, if you want to bond the 2 surfaces (almost the same as creating these rigids, but easier to setup)
- linear, with no friction, if you want to allow the plates to slide over each other, but not opening/closing in normal direction
- nonlinear, if you want to allow both sliding and separation/closing depending on the loading scenario (this might also include friction)
from top to bottom, the fidelity increases, but also the computational cost increases too.
So it depends on what you want.
If you decide to go by contacts, take a look at OptiStruct documentation and tutorials.
0