How to reduce penetration
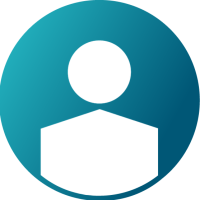
Hello,
May I ask your favor regarding contact and reaction force?
1. Regarding contact (penetration)
1-1) I am solving excavator model which is passing over blocks. As you can see in below picture (section cut view to see penetration) there are several penetrations. I solved several times by changing contact stiffness K (F=K*z^exp) but those were not worked properly. I tried within 1000~3000 for K and time step 0.0005~0.0003 (too long solving time if use 0.0001). Can you advise me how to reduce penetration?
1-2) As you can see in picture in below right, too much penetration was made for 0.01 second. There are around 50 sub steps between 4.94 and 4.95 second. And average step size is 2.44E-5. Should I reduce step size more? or is there any reason and countermeasure for this kind of result?
1-3) I saw Advanced option panel for contact in MotionView. Is this helpful to resolve above problem? I tried with checking them but I was faced an error. Could you explain me the function of the option? or Could you let me know the link describing detail explanation?
2. Reaction force
I am comparing Roller's reaction forces between test and simulation. Reaction force by simulation is 2 or 3 times higher than that of test. All parts are composed by rigid body, including ground. Length of ground is around 30m and I installed bushing(3E5N/mm for translational, 1E15N/mm for rotational) on the ground to reduce reaction force but it was not enough to reduce reaction force (ground deflect too much if use weaker bushing). Do you have this kind of experience? and could you share the experience how did you resolve this kind of problem (very higher force than real)?
Thank you and Merry Christmas & Happy New Year.
Best Answer
-
Hi Yoseob,
Full vehicle contact models are quite complex, especially tracked models, and can lead to this behaviour that you are currently seeing. The contact definition as well as the CAD are critical elements to ensuring a smooth and accurate simulation. If you haven't already, I would review the MotionSolve documentation for 3D contacts best practices here:
Contact Penetration
Incremental changes to the contact stiffness and stiffness exponent is a good starting point. Since you are still seeing penetration, then another area to investigate would be the quality of the CAD used for the obstacles and tracks. If the mesh sizing is very coarse, then there is a higher probability of penetration to occur. I believe this is what is occurring in the third picture. Try a finer mesh for the 3D contact entities either in HyperMesh or change the mesh coarseness for contacts in the Entity Editor for the Graphics body in MotionView:
Additionally, I would simplify the geometry on the bottom of the track as it looks like there is a hole in it. By making that flat, you will improve contact and not reduce the ability to traverse the block.
The Advanced options will help to improve the simulation as well. By enabling "Find precise contact event", once the solver detects contact it will rewind slightly to make sure that contact did not occur a split second earlier. This can help correct poor integration time step settings. As well, "Change simulation max step size" will allow you to set a much smaller step size when contact is detected, so if there is a portion of the simulation before contact is made, you can set a coarse step size initially that will be corrected when contact begins. This can save simulation time potentially. Lastly, you can change where the contact force is computed, either at the center of the mesh element or at the nodes. Changing the location may improve contact detection, but it may effect the force orientation during contact.
The documentation for these options can be found easily here: https://help.altair.com/hwsolvers/ms/topics/solvers/ms/best_practices_for_modeling_3d_contacts_ms.htm?zoom_highlight=contact
Reaction Force
It is typical to see higher reaction forces when dealing with completely rigid models that also experience 3D rigid contact. If the contact forces are extremely sharp, then that will propagate into your roller bearings. I would look into the damping properties for your contacts to see if you can smoothen out the impact using the damping coefficients. The high reaction forces you are seeing is likely due to the less than ideal contact behaviour you have highlighted in the pictures. This small obstacle contact you are trying to simulate is not ideal, and you may want to explore allowing more penetration between the track and the obstacle to help smoothen out this simulation as well.
I would not advise connecting your ground surface to Ground through a bushing, as this is merely covering up an issue from the contact approach in the model.
Hope this helps!
Adam Reid
0
Answers
-
Hi Yoseob,
Full vehicle contact models are quite complex, especially tracked models, and can lead to this behaviour that you are currently seeing. The contact definition as well as the CAD are critical elements to ensuring a smooth and accurate simulation. If you haven't already, I would review the MotionSolve documentation for 3D contacts best practices here:
Contact Penetration
Incremental changes to the contact stiffness and stiffness exponent is a good starting point. Since you are still seeing penetration, then another area to investigate would be the quality of the CAD used for the obstacles and tracks. If the mesh sizing is very coarse, then there is a higher probability of penetration to occur. I believe this is what is occurring in the third picture. Try a finer mesh for the 3D contact entities either in HyperMesh or change the mesh coarseness for contacts in the Entity Editor for the Graphics body in MotionView:
Additionally, I would simplify the geometry on the bottom of the track as it looks like there is a hole in it. By making that flat, you will improve contact and not reduce the ability to traverse the block.
The Advanced options will help to improve the simulation as well. By enabling "Find precise contact event", once the solver detects contact it will rewind slightly to make sure that contact did not occur a split second earlier. This can help correct poor integration time step settings. As well, "Change simulation max step size" will allow you to set a much smaller step size when contact is detected, so if there is a portion of the simulation before contact is made, you can set a coarse step size initially that will be corrected when contact begins. This can save simulation time potentially. Lastly, you can change where the contact force is computed, either at the center of the mesh element or at the nodes. Changing the location may improve contact detection, but it may effect the force orientation during contact.
The documentation for these options can be found easily here: https://help.altair.com/hwsolvers/ms/topics/solvers/ms/best_practices_for_modeling_3d_contacts_ms.htm?zoom_highlight=contact
Reaction Force
It is typical to see higher reaction forces when dealing with completely rigid models that also experience 3D rigid contact. If the contact forces are extremely sharp, then that will propagate into your roller bearings. I would look into the damping properties for your contacts to see if you can smoothen out the impact using the damping coefficients. The high reaction forces you are seeing is likely due to the less than ideal contact behaviour you have highlighted in the pictures. This small obstacle contact you are trying to simulate is not ideal, and you may want to explore allowing more penetration between the track and the obstacle to help smoothen out this simulation as well.
I would not advise connecting your ground surface to Ground through a bushing, as this is merely covering up an issue from the contact approach in the model.
Hope this helps!
Adam Reid
0 -
Adam Reid_21142 said:
Hi Yoseob,
Full vehicle contact models are quite complex, especially tracked models, and can lead to this behaviour that you are currently seeing. The contact definition as well as the CAD are critical elements to ensuring a smooth and accurate simulation. If you haven't already, I would review the MotionSolve documentation for 3D contacts best practices here:
Contact Penetration
Incremental changes to the contact stiffness and stiffness exponent is a good starting point. Since you are still seeing penetration, then another area to investigate would be the quality of the CAD used for the obstacles and tracks. If the mesh sizing is very coarse, then there is a higher probability of penetration to occur. I believe this is what is occurring in the third picture. Try a finer mesh for the 3D contact entities either in HyperMesh or change the mesh coarseness for contacts in the Entity Editor for the Graphics body in MotionView:
Additionally, I would simplify the geometry on the bottom of the track as it looks like there is a hole in it. By making that flat, you will improve contact and not reduce the ability to traverse the block.
The Advanced options will help to improve the simulation as well. By enabling "Find precise contact event", once the solver detects contact it will rewind slightly to make sure that contact did not occur a split second earlier. This can help correct poor integration time step settings. As well, "Change simulation max step size" will allow you to set a much smaller step size when contact is detected, so if there is a portion of the simulation before contact is made, you can set a coarse step size initially that will be corrected when contact begins. This can save simulation time potentially. Lastly, you can change where the contact force is computed, either at the center of the mesh element or at the nodes. Changing the location may improve contact detection, but it may effect the force orientation during contact.
The documentation for these options can be found easily here: https://help.altair.com/hwsolvers/ms/topics/solvers/ms/best_practices_for_modeling_3d_contacts_ms.htm?zoom_highlight=contact
Reaction Force
It is typical to see higher reaction forces when dealing with completely rigid models that also experience 3D rigid contact. If the contact forces are extremely sharp, then that will propagate into your roller bearings. I would look into the damping properties for your contacts to see if you can smoothen out the impact using the damping coefficients. The high reaction forces you are seeing is likely due to the less than ideal contact behaviour you have highlighted in the pictures. This small obstacle contact you are trying to simulate is not ideal, and you may want to explore allowing more penetration between the track and the obstacle to help smoothen out this simulation as well.
I would not advise connecting your ground surface to Ground through a bushing, as this is merely covering up an issue from the contact approach in the model.
Hope this helps!
Adam Reid
Hello Adam,
Thank you for your detail advices.
I already read linked document several times, it is very nice and valuable document. thank you.
I am not sure my ground should be set as rigid because the ground is thick steel plate seated on concrete (not bonded). And now I understand the contact event option with your explanation. I will try again with your advices.
Thank you and Happy New Year, Adam
1