How to simulate quenching of an aluminum profile?
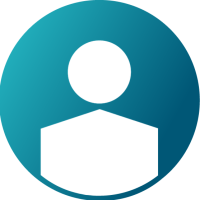
Hello everyone,
For my master’s thesis, I am currently conducting quenching experiments with aluminum extrusion profiles. The profiles are heated to 550°C and then quenched in a water bath. The profiles are always submerged exactly 90 mm deep, with the water column being 120 mm high and the water temperature set to 20°C.
Now, I need to simulate this process and compare the temperature curves. Since this is my first time working with Hypermesh and I have very little experience with simulations in general, I could really use your help.
Here’s what I’ve done so far:
- I designed the profiles in Inventor and exported them as a STEP file (profile height: 90 mm).
- I imported the file into Hypermesh and created a box to represent the surrounding water (dimensions: 120 x 70 x 70 mm). The water surface and profile surface are aligned at the same level.
- Using Boolean operations, I set up the scenario so that the profile is hollow inside and surrounded by water on the outside.
- I assigned the materials and initial parameters and created a coarse mesh for an initial test simulation.
The problem: When I run the simulation, the temperature curve looks strange. The temperature barely decreases.
My question: What might I be doing wrong? Should I approach the simulation setup differently, or is my current approach basically correct?
I’ve attached a few screenshots to better illustrate the situation.
Thank you very much in advance for your help!
Best regards,
akinh0
Answers
-
What is the boundary condition on the outside of the water (at least the bottom and four sides)? If it's left as just a standard wall, with heat-flux = 0, that is an insulated wall so no heat rejection. Same with the inside boundaries of the extrusion - are those also 0 heat flux walls? If there's no way for the heat to be rejected, the temperature wouldn't change much.
Let's assume outside walls of the water are exposed to a room at temperature 300K. Maybe add convective heat transfer coefficient of 10 W/m2-K. Maybe the same for the inside boundaries of the aluminum extrusion.
There needs to be some mechanism to remove the energy.1 -
Hi acupro,
where can I find such a boundary condition in the software? Is it the "No Slip" boundary condition, or is it an "Advanced Boundary"? Could you explain how to correctly set up the heat transfer to ensure that the convective heat transfer is properly accounted for?
Thanks for your help!
0 -
akinh0 said:
Hi acupro,
where can I find such a boundary condition in the software? Is it the "No Slip" boundary condition, or is it an "Advanced Boundary"? Could you explain how to correctly set up the heat transfer to ensure that the convective heat transfer is properly accounted for?
Thanks for your help!
That will be part of the No Slip boundary condition - if you go to the thermal/temperature portion of that BC definition. You can specify a temperature type or a flux type.
0