How I can define correct stiffness, damping and penetration values at cantact definitons?
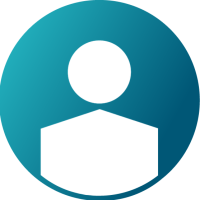
Hi,
I'm trying to find efficieny value of a cycloid gearbox from torques. (A video for working principle: https://www.youtube.com/watch?v=1ijFove42Kw
I'm using Altair Inspire Motion for this subject. There are contacts between cycloid gears and housing pins.
I'm not sure about stiffness, damping and penetration values at contacts. How can I determine these?
Best regards.
Hakan GÜNEŞ
Answers
-
Hello, Hakan,
The default values used by Inspire should always be viewed as starting points for the contact modeling. How heavy the parts are, how fast they are moving relative to one another, and what the geometry looks like at the contact interface are all things that affect the behavior of the contact. Contact modeling in multi-body simulation is different from formulations done like in FEA. For FEA, stiffness and damping are based on material deformation. Units of stiffness are N/mm^2. For rigid multibody contact, Inspire uses linear (spring) stiffness (N/mm). If you do not have actual test data to correlate with, some experimentation and focus on changing the right values, based on behavior, can lead to more efficient contact modeling with good results.
For the cycloid example you referred to (steel on steel), you can begin with the defaults, but I imagine you will see some larger penetrations between contacting parts. From there, I would suggest starting with Stiffness=1e5 N/mm and a Damping of 1 N-s/mm. Then, you should monitor your output by plotting Contact force and Penetration depth for the contact. Although it may be very small, there will always be a non-zero value for penetration (it is not an FEA contact, it is a math approximation of similar behavior). However, it should be reasonable for the given problem. For example, for large scale problems (heavy machinery) values of 0.5 mm might be acceptable. For smaller systems, such as a latch mechanism, 0.05 mm is acceptable. The stiffness (along with the applied contact force) will control the penetration amount. Any noise or bounce effect from touching components could indicate over or underdamped. If so, experiment with changing damping a couple values above the default, say 5 or 10 and monitor noise and Penetration Velocity. If you are using version 2022, I would suggest turning on the Active Contact Iteration option under the motion Run Settings --> Contacts. This feature helps converge models faster and smoother when there is continuous contact involved. I would not initially suggest changing the Exponent or the Penetration Depth entries, only Stiffness and Damping.
Overall, the default values will get you in the general area. From there, adjustments based on resulting behavior can be done to fine tune.
Regards,
Scott Z
0 -
Hakan,
One other thing... the Penetration Depth property is NOT the amount of penetration you want to allow between the two parts. Instead, it is the rate of increase in damping from 0 to full damped value, as the parts penetrate to the amount specified under Penetration Depth.
Regards,
ScottZ
0 -
Hello Scott,
Before I read your reply, at the end of many attempts I got properly results with stiffness 100000 N/mm, damping 1 N.s/mm, exponent 2,1 and peneration 0,1mm. I'm happy to see my values and your suggested values are almost the same. I will try with 0,05mm penetration value too.
Thanks for your reply and help.
Regards,
Hakan GÜNEŞ
0