Free Size optimisation
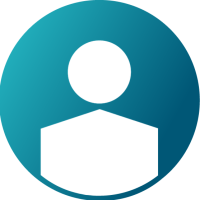
Hi,
I am running a free size analysis on a 1800 mm DIA tube using a static linear load step with a GRAV load card as it is a self weight problem. The tube is simply supported and 33 000 mm in length.
When I create a displacement constraint the constraint cant be created as the load step is not compatible with the design variable, see below.
The model is a PSHELL surface model.
I am attempting to minimize the volume fraction of the tube to reduce weight based on the displacement. The design variable is also using a zone based approach to keep section at the same thickness and the design variable has a stress constraint on the DESVAR card.
How can this static load case not be accepted by a simple dconstraint set up?
Thank you
Best Answer
-
hi,
just a sanity check: are you sure you are using 'Static Displacement' response? and not others like FRF displacement.
How about your loadstep setup. Is it set to 'linear static'?
Can you share the model (.fem)?
0
Answers
-
hi,
just a sanity check: are you sure you are using 'Static Displacement' response? and not others like FRF displacement.
How about your loadstep setup. Is it set to 'linear static'?
Can you share the model (.fem)?
0 -
I used a static displacement and a linear static analysis.
I cant share the model as it is a live project unfortunately and I can not share the geometry below the tube.
I got the model running, but the displacement in the the iterations are too high, see below, +2700 mm. I would like the algorithm to stay below 350 mm deflection which will help it converge faster.
The free size card allows me to add a stress constraint directly in the design variable set up, but now the optimisation starts with a very large displacements and runs forever.
0 -
Casper Kruger said:
I used a static displacement and a linear static analysis.
I cant share the model as it is a live project unfortunately and I can not share the geometry below the tube.
I got the model running, but the displacement in the the iterations are too high, see below, +2700 mm. I would like the algorithm to stay below 350 mm deflection which will help it converge faster.
The free size card allows me to add a stress constraint directly in the design variable set up, but now the optimisation starts with a very large displacements and runs forever.
take a look at your constraint.
you've asked for a LOWER BOUND of 350mm.
It should be UPPER BOUND
0 -
There is currently only the stress constraint added in the design variable card. It does not allow me to add a displacement constraint.
0 -
Casper Kruger said:
There is currently only the stress constraint added in the design variable card. It does not allow me to add a displacement constraint.
A 350 N/mm² von mises constraints built into the DES VAR
0 -
Casper Kruger said:
There is currently only the stress constraint added in the design variable card. It does not allow me to add a displacement constraint.
it is really strange that you can't pick the displacement response in your constraint.
What if you create a 'compliance' response and constraint it to a certain value.
Compliance is a global measure of flexibility of your structure. So if you keep it under some value, it will help you control your displacements indirectly.
Let's say your compliance is 50000 in your current model. Add a constraint so that it keeps below 40000, for example.
0 -
Where can I find the global compliance of the structure in Optistruct, as the geometry downstream is more complex and can not be easily calculated?
The model converged, but the non design space attempted to optimise, where can I exclude these elements when using a free size optimisation?
This seems to be the issue as the stress constraint did the job. The area of concern did not deflect more than 400 mm
0 -
Casper Kruger said:
Where can I find the global compliance of the structure in Optistruct, as the geometry downstream is more complex and can not be easily calculated?
The model converged, but the non design space attempted to optimise, where can I exclude these elements when using a free size optimisation?
This seems to be the issue as the stress constraint did the job. The area of concern did not deflect more than 400 mm
the global compliance values are calculated when you perform the analysis. You will find "iteration XX" , and there's the mass and the compliance for each static loadcase in the .out file.
Free-size design space is based on the property selected. So in order to segregate a few elements you need to move them to another comp/property in your model.
0 -
I only only selected the property of the tube and the tube is in its own component collector. Any reason why the free size will alter any elements not part of the property selected? Should the remaining elements be classed as non design space?0