RePosting: How to model overhead power line in FLUX
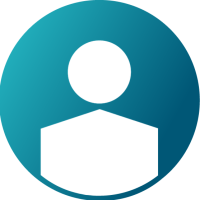
Reposting as I didn't get enough feedback. I believe I may have posted this question in a wrong forum or thread.
Dear Experts,
I am in need to model E-fields emanating from a 3-phase, 60 Hz, 80m length and 10m pole height overhead power line. Measurement point is at 2.5 m from ground. Moreover, I am required to find out the the variation of the E field from one pole to the other along the conductor path. Which I guess would have exponential raise and fall profile. I think this situation can be best modelled in 3D environment. or Is it? Is this best suited for any other feature of FLUX or Altair Suite that I don't know about. Please advise.
When I attempted to model this in 3D, I learnt that meshing takes very long and the model gets heavier. Is there any other quick and optimal manner to simulate long power lines in FLUX? Please advise.
In 3D Steady state AC electric model, What is the reference point for the voltages? is it Infinite? Can I specify any other geometry to be my reference? for example a ground plane? Please advise.
Thanks and Best Regards
Balaji
Best Answer
-
Hello,
you can follow the instructions I attach here in general for meshing and controlling the mesh with meshpoints only. This is to assign a given mesh size to each part.
In your case, you also need to define an extrusive mesh:
- Make sure your volume is ok to use extrusive mesh. It needs to be a constant section without change along the length
- Create a geometric transformation defining your extrusion. For instance, 10m along y axis
- Create a mesh generator of "extrusive" type and assign it to the volume
- check that it works by meshing lines only. If not, you may need to adjust the geometry or check the transformation is correct for that volume
- Once it works, you can add a single mesh line to one of the extrusion lines. It will control the number of elements along the extrusion. Arithmetic for instance allows you to define a number of elements/layers along the extrusion.
I hope this helps.
2
Answers
-
Hello,
About your application, I think that it depends on the frequency and dimensions. In Flux we consider quasi static hypothesis which means there is no wave propagation. Otherwise you may need to use FEKO in this case if propagation plays a role.
I would say in general that your model should probably be done first in 2D to see the field from the cable line. About the two poles model, that one I guess Flux3D would be needed if the hypothesis are ok as explained before. The mesh would be very sensitive. Ideally an extrusive mesh with long elements on the cable and a large mesh for the whole air and ground around.
PS: try not to repost on the forum to avoid double posts and confusion
1 -
Hi Simon Guicheteau,
Thank you very much for your response. Apologies for the confusion created with the double posts. I was desperate to find the solution.
I did build and run 2D steady state AC models to get a sense of E-field. What I am really interested to see though is the variation in field strength when traversed from one pole to the another.
Yes, The mesh of 3D model is really sensitive. It takes much longer compared to 2D and oftentimes the model gives an error asking to check the mesh on a given face. It seems unpredictable.
As you can imagine the geometry is pretty simple - 3 Conductors of 40/70/100m length with 1/1.5/8m spacing surrounded by 10/20/30m thick air cylinder. So far, I only tried using default mesh settings - 'mesh domain'. I'd really love to customize the settings to mesh this geometry optimally. Could you kindly share any documentation or manual or notes on how do I define long elements on the conductors and large elements for the surrounding air? That I believe is a relevant solution to my problem at hand.
This would be greatly helpful.
Thank you very much in advance
Balaji V Gollapalli
0 -
@Simon Guicheteau @Simon Guicheteau @Farid zidat @Abdesssamed soualmi @Abdessamed
May I ask if any one could help me find any documentation or manual or notes about what mesh settings would be appropriate to mesh the geometry at hand?
The geometry is composed of a simple 3 cylindrical conductors of 40/70/100m in length with 1/2.5/8m spacing between them surrounded by a 10/20/30m thick air cylinder (Refer to posts above for more context). Default mesh settings does not seem to work. Mesher throws an error arbitrarily asking me to check the mesh on one of the faces. And when it manages to mesh, it takes significantly longer (3-4 hours). Looking forward to hearing from you.
Thanks in advance
Balaji
0 -
@Simon Guicheteau @Simon Guicheteau @Farid zidat @Abdesssamed soualmi @Abdessamed
Hi All,
Greetings. Hope you are having a great day. Gentle reminder. Could any one please help me find relevant information about the meshing technique recommended above? With all respect, I hope to test the recommendation before marking it as the Correct Answer.
Thanks and Best Regards
Balaji
0 -
Hello,
you can follow the instructions I attach here in general for meshing and controlling the mesh with meshpoints only. This is to assign a given mesh size to each part.
In your case, you also need to define an extrusive mesh:
- Make sure your volume is ok to use extrusive mesh. It needs to be a constant section without change along the length
- Create a geometric transformation defining your extrusion. For instance, 10m along y axis
- Create a mesh generator of "extrusive" type and assign it to the volume
- check that it works by meshing lines only. If not, you may need to adjust the geometry or check the transformation is correct for that volume
- Once it works, you can add a single mesh line to one of the extrusion lines. It will control the number of elements along the extrusion. Arithmetic for instance allows you to define a number of elements/layers along the extrusion.
I hope this helps.
2 -
Thank you so much Simon for the guidance. This is helpful.
I also had a demonstration discussion with one of the technical experts. With this method, I could control the mesh elements very well.
0 -
@Simon Guicheteau The above instruction 3 months ago. Did not yield correct Result. I think the FLUX solver is wrong or it is not suitable to solve this particular use case or I may be doing something wrong. There is a HUGE variation between FLUX results and CDEGS (Current Distribution, Electromagnetic Fields, Grounding and Soil Structure Analysis) result. CDEGS is another software that I used to compare FLUX results.
Moreover There is significant variation between the identical models run in FLUX 3D Vs 2D. We spent 4 months trying to work this use case in FLUX.
Furthermore, The result differs significantly from the measured data from our experiments. Could you please lend any further technical help to resolve this issue?
We were deeply disappointed at how FLUX performed compared to competitor software. This would make it harder to convince our management to renew licenses for next year.
0 -
The variation in results from 3D and 2D models of overhead power lines is due to different meshing in both models.
Since the mesh density and type of mesh elements plays a significant role in Flux computations, after using 2nd order mesh elements and same mesh density for both 2D and 3D models, the variation has been reduced to <4%
Please refer to Service now ticket CS0248014 for more information and Flux models for reference.
Thank you,
Lavanya
0