How can I better constrain a moving part when it comes into contact with particles in a Hyperworks-EDEM co-simulation?
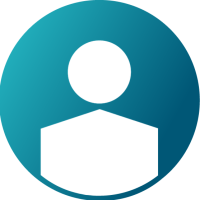
Hello,
I have successfully got a Hyperworks-EDEM co-simulation running thanks to very useful Altair support, however the simulation is not running realistically.
I have meshed an agricultural spring tine using Hypermesh. The geometry has one rigid RBE2 spider at a point where the tine would be fixed and dragged from machinery (I want this to stay in a fixed position throughout the simulation). There are a total of 3 interface nodes all of which is seen beneath.
I have assigned a material and thickness to the 2D automesh. The mesh was imported into MotionView and a flexbody created using Optistruct (built in FlexPrep). In MotionView a joint was assigned to the Interface node at the rigid spider and given a motion (5km/h velocity). The geometry has been coupled with EDEM and is dragged through a soil bin, however the tine starts off fine until it begins to hit the soil where it appears to vibrate excessively and breaks the rigid body constraint it has (the behaviour is shown beneath x3). The same time has been physically tested and works in real life using the soil and depth I am using. The tine is 60mm wide 5mm thick and will be 70mm deep in the soil so the force shouldn't be excessive on the tine geometry.
I have played around with EDEM parameters adjusting the time step and cell size. I have also reduced the density of the soil particles but none of my changes made a difference. I have created a far larger soil bin but that didn't help either. The particles shown are 40mm in diameter, I did run a simulation with particles of 4.75mm (last figure) and it ran far better but the tine geometry still flexed far too greatly and continued to spin around at the end (after pushing the end particles up against the end of the soil bin geometry). I have also tried a 3D tetramesh on Hypermesh so the part is actually physically imported into EDEM with a visibly correct thickness unlike the shell mesh, however I observed the exact same co-simulation result as the 2D mesh (tine spinning around frantically and whacking the particles everywhere). I am convinced it is to do with the tine and its constraints rather than the soil in EDEM but I may be wrong.
I am hoping that someone can point me in the right direction as to why the tine is behaving so oddly and how I can keep it in the soil bin more rather than bouncing out forming unrealistic shapes and lengths (keeping it in the position shown beneath, this was for the smaller particles which worked better but the tine still vibrated backwards and forwards too excessively slapping particles everywhere).
Thanks,
Hugh
Hi Hugh,
I'd recommend looking at time-step and time-step ratio between MotionSolve and EDEM. For time-step you could run it as EDEM alone and just add a simple force to the equipment to push it through the material bed. If you see the same behaviour you can reduce the time-step used in EDEM to aid stability (typically we recommend 20% Raleigh time-step).
If it's OK in EDEM stand-alone you may want to lower the time-step ratio between EDEM and MS, try running both at the same time-step value (1:1 ratio).