Discrepancy between FEM mass and mass during optimization
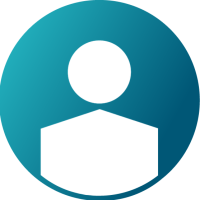
Greetings,
I have a FEM model whose mass calculated by Hypermesh (under Tools > masscalc) is equal to 2.22 kg
I am running a free-size optimization of this model. From the design parameters summary reflected in the *.out file (shown below), the sum of design and non-design mass is equal to 2.51524 kg:
After the iterations begin, the mass registered in iteration 0 is 2.34766 kg
Question: Is it wrong to expect the following: FEM mass = (design + non-design mass) = mass at iteration 0? Why are these values different?
---------------------------
Design Parameters Summary :
---------------------------
Total # of free-sizing design elements : 34684
Total # of free-sizing cards : 1Total Volume of Design Material : 9.3119E-05
Total Mass of Design Material : 4.1904E-01
Volume of Non-Design Material : 7.0062E-04
Mass of Non-Design Material : 2.0962E+00
ITERATION 0
*** INFORMATION # 3454
MPC constraints for subcase 1 will be enforced
with lagrange multipliers.(Scratch disk space usage for starting iteration = 65356 MB)
(Running out-of-core solution)
Objective Function (Min(Max) EQATN) = 4.50698E+07
Maximum Constraint Violation % = 0.12535E+03
Design Volume Fraction = 6.00000E-01 Mass = 2.34766E+00
Answers
-
Update:
During the FE modeling in Hypermesh, design space and non-design space were not explicitly defined by the user.
What is the basis for Optistruct to decide and distinguish between design and non-design spaces?
0 -
Altair Forum User said:
Update:
During the FE modeling in Hypermesh, design space and non-design space were not explicitly defined by the user.
What is the basis for Optistruct to decide and distinguish between design and non-design spaces?
Hi, what do you mean by at red marking?
how did you set up your optimization problem?
0 -
Hi Tinh,
The goal is to optimize the thickness of the insert region subject to stress and mass constraints (I have read that simultaneous definition of mass and stress constraints is not a good idea. I'm still trying to a figure out a way around this). The insert itself has a network of ribs and stiffeners inside which isn't seen in the picture below.
<?xml version="1.0" encoding="UTF-8"?>
During the DV definition, I have chosen the PSHELL cards corresponding to only the insert. This would mean that my design space refers only to the insert and everything else in the model is the non-design space. Am I correct?
Moreover, if the above assumption is correct, the FEM mass of the insert as seen in Hypermesh and the 'total mass of design material' as seen in the *.out file must be equal. Isn't it?
Any inputs or critiques are highly appreciated. Thank you!
0 -
Yes, you are correct.
In hypermesh tools>masscalc you select only designed PSHELLs to get designed mass, it should be equal to 'mass of design material' in .out file
0 -
Altair Forum User said:
I have a FEM model whose mass calculated by Hypermesh (under Tools > masscalc) is equal to 2.22 kg
I am running a free-size optimization of this model. From the design parameters summary reflected in the *.out file (shown below), the sum of design and non-design mass is equal to 2.51524 kg:
After the iterations begin, the mass registered in iteration 0 is 2.34766 kg
But I get different masses as shown above. What might be the reason?
0 -
Reasons might be you calculate wrong or hypermesh calculates wrong or optistruct calculates wrong
0 -
Haha, it doesn't seem too likely that Hypermesh or Optistruct would be wrong. Maybe an understanding of how Optistruct segregates design and non-spaces could elp.
0