tied interface and AMS
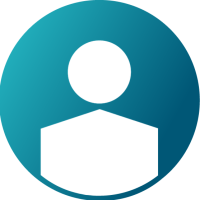
Hi,
I am trying to run a model with tied interface (Type 2) and AMS. The interface is defined with contact surface as master and nodes on the slave side.
During starter the following warning appears:
WARNING ID : 852
** WARNING SLAVE NODE OF AN INTERFACE TYPE2 & AMS
and during computation:
WARNING INTERFACE 2
NODE xxx DE-ACTIVATED FROM INTERFACE
Can this deactivation of slave nodes be avoided when using AMS and type 2 interface? The same model was run successfully using DT/NODA/CST.
Answers
-
Actually, the deactivation of nodes was due to another interface (type 7) and it was solved by setting the Irem_gap to 1.
I would still like to know the reason of WARNING ID : 852
0 -
Hi Ivan,
In AMS for RADIOSS, a node cannot be slave to a Type 2 interface and a Type 7 interface at the same time. A node can therefore be slave, either of type 2 or of type 7. Please correct your modeling in order to solve this observed behavior.
0 -
Hi George,
Thanks for the tip. The manual also suggests this contact deactivation can be avoided by using Spotflag=25 or 26 (TYPE2 penalty formulation).
Both methods avoid WARNING ID : 852 ** WARNING SLAVE NODE OF AN INTERFACE TYPE2 & AMS; however some slave nodes of type 7 are still de-activated during simulation, eventhough they are not referenced in type 2. So this de-activation is probably caused by type 7 interface definition (ouput file):
INTERFACE NUMBER : 2 kontakt
TYPE.EQ.7 PARALLEL/AUTO IMPACTINGBOUND. COND. DELETED AFTER IMPACT IN X DIR 0
SLAVE NODE (1:YES 0:NO) Y DIR 0
Z DIR 0
BOUND. COND. DELETED AFTER IMPACT IN X DIR 0
MASTER NODE (1:YES 0:NO) Y DIR 0
Z DIR 0
STIFFNESS FACTOR. . . . . . . . . . . . . 1.000000000000
STIFFNESS FORMULATION. . . . . . . . . . 4
2,3,4,5 : STIFFNESS IS COMPUTED FROM STIFFNESS ON MASTER SIDE
AND STIFFNESS AT SLAVE NODES
1000 : STIFFNESS IS COMPUTED FROM STIFFNESS ON MASTER SIDE
MINIMUM STIFFNESS. . . . . . . . . . . . 0.000000000000
MAXIMUM STIFFNESS. . . . . . . . . . . . 1.0000000150475E+30
FRICTION FACTOR . . . . . . . . . . . . . 0.4000000059605
VARIABLE GAP FLAG . . . . . . . . . . . . 1
MINIMUM GAP . . . . . . . . . . . . . . . 0.1000000014901
MAXIMUM GAP (= 0. <=> NO MAXIMUM GAP) . . 1.0000000150475E+30
%MESHSIZE TAKEN INTO ACCOUNT FOR . . . .
CALCULATION OF MAXIMUM GAP(IGAP = 3). . . 0.000000000000
FLAGREMNODE : NOT CONSIDER NEIGHBORING . .
NODES IN CASE OF ELEMENT SIZE < GAP VALUE 1
DE-ACTIVATION FLAG IF CONFLITING W/ TYPE2 3
GAP SCALE FACTOR. . . . . . . . . . . . . 0.000000000000
START TIME. . . . . . . . . . . . . . . . 0.000000000000
STOP TIME . . . . . . . . . . . . . . . . 1.0000000150475E+30
BUCKET FACTOR . . . . . . . . . . . . . . 0.2000000029802
DE-ACTIVATION OF INITIAL PENETRATIONS . . 1
MAXIMAL INITIAL PENETRATION FACTOR. . . . 0.000000000000
CRITICAL DAMPING FACTOR . . . . . . . . . 5.0000000745058E-02
FRICTION CRITICAL DAMPING FACTOR. . . . . 0.000000000000
QUADRATIC DAMPING FLAG. . . . . . . . . . 0
FORMULATION LEVEL . . . . . . . . . . . . 0
MEAN POSSIBLE NUMBER OF IMPACT/NODE . . . 4DELETION FLAG ON FAILURE OF MASTER ELEMENT (1:YES-ALL/2:YES-ANY) : 1000
FRICTION FORMULATION: INCREMENTAL (STIFFNESS) FORMULATION
FRICTION FILTERING FLAG. . . . . . . . . 0
FILTERING FACTOR . . . . . . . . . . . . 1.000000000000FRICTION MODEL 0 (Coulomb Law) :
FRICTION COEFFICIENT . . . . . . . . . 0.4000000059605SLAVE SURFACE INPUT BY NODES
MASTER SURFACE INPUT BY SEGMENTS0 -
Hi Ivan,
The possible workaround is setting /INTER/TYPE2 Spotflag to 25 (to switch from kinematic to penalty based tied interface formulation) and it will be affected only to the nodes referenced to TYPE2 interface.
The /DT/AMS will increase the time step of small elements. The warning message NODE xxx DE-ACTIVATED FROM INTERFACE you are getting is due to the kinematic time step of the interface. It is because that the node is penetrating too far into the gap. You can try increasing the Gapmin in your TYPE7 interface which will allow the contact to work sooner and prevent node from penetrating so far. Or you could try making the interface stiffer, Istf=3 which uses the maximum stiffness of the slave and master.
0 -
Thanks for being helpful as usual, George.
The interface could also be made stiffer by increasing stiffness scale factor Stfac.
0 -
Increasing the min_gap worked, but during computation the energy error suddenly drops to -99.9% and unrealistic stresses propagate through the structure, when compared to the run with traditional mass scaling (at 1/10 the timestep of AMS).
0 -
Hi Ivan,
Please ensure that fully integrated elements are used for the run. Also check the hourglass energy in the model.
Can you please share the engine out file?.
0 -
Hi Ivan,
Please share the model files through the secure dropbox link.
0 -
Hello,
I have sent the requested files to dropbox.
Some parts were modeled with under-integrated elements but hourglass energy is constant throughout.
I also ran the fully integrated model and the same issue occurs.
0 -
Comparing energy error time history with animation it became apparent there was a modeling issue: shell elements were penetrating into solid edges.
0