SPH Contact Problem
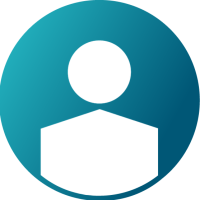
Hello,
I am working on sloshing motion of water in a tank.
- Although there is Type7 contact between the shell element and the SPH particles, I witnessed some particles passing through. Is there any other contact type that can be used instead of Type 7?
- Or how do I fix this situation?
Thank you.
Regards,
Answers
-
Hi,
TYPE7 is the correct contact. There are a few examples in the help that show contact between SPH and structures. Can you provide a simple model to show the issue you are having?
RD-E: 4900 Bird Strike on Windshield describes the following,
Contact between SPH bird and structure and impact setup
- Interface TYPE7 is selected to simulate the contact between SPH bird and windshield structure. The windshield structure is selected as main surface and the SPH bird as secondary nodes.
- Igap=1 (use variable gap + gap scale correction + considering mesh size). The gap is ½ particle diameter + ½ thickness of the target. This is the physical value for contact.
- The stiffness between bird and windshield structure are quite different. In order to get results closer to reality, set Istf=0 and Stfac=0.1. This means interface stiffness equals to 0.1 times stiffness of main side (structure).
Thanks,
Andy
1 -
Andy_20955 said:
Hi,
TYPE7 is the correct contact. There are a few examples in the help that show contact between SPH and structures. Can you provide a simple model to show the issue you are having?
RD-E: 4900 Bird Strike on Windshield describes the following,
Contact between SPH bird and structure and impact setup
- Interface TYPE7 is selected to simulate the contact between SPH bird and windshield structure. The windshield structure is selected as main surface and the SPH bird as secondary nodes.
- Igap=1 (use variable gap + gap scale correction + considering mesh size). The gap is ½ particle diameter + ½ thickness of the target. This is the physical value for contact.
- The stiffness between bird and windshield structure are quite different. In order to get results closer to reality, set Istf=0 and Stfac=0.1. This means interface stiffness equals to 0.1 times stiffness of main side (structure).
Thanks,
Andy
Hi @Andy ,
Firstly, thank you very much for your helps.
I did not come across this problem in simple models. I cannot share the complex model due to information confidentiality.-
When creating SPH partical in a closed tank, I consider checking the Igap and Stfac values for the particles formed close to the walls. Could it be due to this?
-
Could this problem be caused by the particles being too fast?
-
Is type 7 contact type also suitable between 3D elements and SPH particles? (For example; tetramesh bethween SPH partical)
- Suppose there is a cross section like in Figure 4. Can SPH particles escape from contact areas?How can I prevent this? ( As the only remedy, I closed that area with the "ruled" command. )
Thank you.
Regards,
0 -
Hi,
Answering your question.
1) If the contact is too small then it could be an issue. What is your GAPmin value? If you don't define it then Radioss calculates it and puts it in the starter output file. What are you using for Igap, Istf, and Stfac?
2) Yes if particles move too fast then that might be an issue but if this is tank sloshing then that should not be a problem.
3) Yes
4) If particles are going out the space between what you have labeled as shell elements, I think you could create shell elements and assign /MAT/VOID and /PROP/VOID to them. The elements will not have any structural stiffness but will have contact stiffness based on the values you enter in /MAT/VOID and /PROP/VOID. This should prevent the particles from escaping.
1 -
Ovunc2 said:
Hi,
Thank you @Andy . Your answers are very helpful to me.
I' m using Stfac =1 , Fric = 0,1 , Gapmin= 0,1 .
How much do you think I should lower these rates?
Best regards,
Hi,
If your units are mm then Gapmin=0.1 seems small assuming your model is some sort of fuel tank. What is your Igap value?
Thanks,
Andy
0 -
Ovunc2 said:
Hi,
Thank you @Andy . Your answers are very helpful to me.
I' m using Stfac =1 , Fric = 0,1 , Gapmin= 0,1 .
How much do you think I should lower these rates?
Best regards,
Hi
Sorry for the late reply. What value are you using for Igap? I would follow these guide lines,
Set Gapmin= ½ particle diameter + ½ thickness of the tank.
Stfac=0.1 is typical but can be increased in some situations.
I think Fric=0 would be better for friction between the water and tank.
Thanks,
Andy
0