Reaction forces on Rb master node
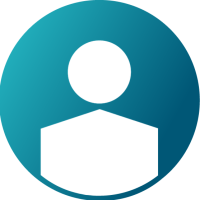
Answers
-
Hi Karthic,
You can create an output block (Analysis>>Output block>>select node from the the option) for the node, and provide the required output request, that is REACX, REACY or REACZ which are the X, Y and Z X reaction force on the node. Please go through /TH/NODE in the Help Menu which explains about the various output variables available for the time history for nodes.
You can also go through this webinar which shows creating output blocks in RADIOSS: https://www.youtube.com/watch?v=Ef7Spn-j7fA&index=6&list=PL1u26y75SCrA_BOCLaSewVCNY7xRvCTnA
0 -
Thank you George
/emoticons/default_smile.png' srcset='/emoticons/smile@2x.png 2x' title=':)' width='20' />
0 -
Hi George,
I got the reaction force as you suggested.
What is the allowable limit for the Energy error %(for Quasi static case) in engine out file.
whether Negative is preffered rather than positive ?
0 -
Hi Karthic,
The Energy Error computed by RADIOSS is a percentage. If the error is negative, it means that some energy has been dissipated, which can be due to contact friction or hourglassing. In case of under integrated elements (Belytschko shells, solids with 1 integration point), the Hourglass energy can also explain a negative Energy Error since it is not counted in the energy balance. The normal amount of Hourglass energy is about -10% to -15%.
If the error is positive, there is an energy creation. In case of using QEPH shell formulation or fully integrated elements, the Energy Error can be slightly positive since there is no Hourglass energy and the computation is much more accurate. An error of +1% or +2% is acceptable. If the positive energy error is greater than 2%, the source of this energy has to be identified. Incompatible kinematic conditions can lead to such a situation.
0 -
-
Hi,
The recommended value for energy equation is as follows:
(Hourglass energy +contact energy)/TE this should be less than 15 %
In your case this i very high as contact energy is almost same as TE and even higher than it.
It seems there are penetrations in the model. Check this in hypercrash. Also check whether any incompatible boundary conditions are there in model.
0 -
I have used Ishell 24(QEPH) and P14 solid hexa elements(P solid14).
0 -
Thank you Gopal Rathore
0 -
HI,
I dont find any penetration/ intersection of mesh in the contacts, penetration is found in parts that do not have contact. will this cause problem?
'NO TRUE INCOMPATIBLE KINEMATIC CONDITION' message in out file.
Can you please help me with this issue
0 -
Hi,
Can you see anything from the animation files. Have you checked the penetration in hypercrash?
Also what type of simulation you are running.
0 -
Hi Karthic,
The contact energy seems to be in a higher side in the model. Please check the contact defined and the contact parameters in the model.
Can you please share the model file through secure dropbox so that we can review it.
0 -
Hi George,
ya contact energy is drastically increasing. I have shared the model. Please guide me.
0 -
Hi Gopal,
Its quasi static simulation. Snap fit problem. my simulation is ok. but contact energy is too high.
0 -
Hi,
It seems you are using plastic material in model and this results in low contact stiffness which raises the contact energy and to control it , I think you need to assess the contact parameters used in interfaces.Can you send the file in 13 version
0 -
Hi Karthic,
In the model, please review the ring component material. And there are initial penetrations in the interface. Please clear those, review the material and try running the analysis.
Please go through this webinar https://www.youtube.com/watch?v=L1vM2Qp9efE&index=7&list=PL1u26y75SCrA_BOCLaSewVCNY7xRvCTnA which explains about the final model checking in HyperMesh.
0 -
Thank you.
The ring component is special spring steel. We dont Know the strain at UTS. So i used a value from google.
0 -
HI,
Even after clearing the penetration in model and material check, i am facing the same issue of Higher negative error.
0 -
Hi Karthic,
Please review the results to see if they appear realistic. Negative Energy Error represents energy dissipated from the system and this can be from many sources including plastic deformation and Hourglass energy. If you are not expecting high plastic deformation then hourglass energy can result in higher negative energy error.Only user can decide the acceptable range with negative energy error.
Please share the engine out (_0001.out) file.
0 -
Hi George,
Hourglass energy in the plot is very minimum when compared to the IE(Strain energy in the ring). Let me share the engine out files for the model with penetration and with out penetration. I even tried shell elements for the outer seelve keeping the ring alone as solid, but it didnt work. using fully Integrated solid element is taking weeks to compute.
my ultimate goal to find the force required to work out the snap. now i am geeting 10N as result. Expecting 45-50 N.
0 -
The History out results are realistic except the contact energy.
0 -
-
Thanks a lot
0 -
Hi George,
What about the energy error. Can u pls share the engine out file and Engine file.
0 -
HI George,
The files you asked for. I even tried it with Tetra mesh to avoid hourglass. Full IP solid elemets taking huge time to solve.
0 -
Hi Karthic,
Solid elements will take more time for computation. Use Isolid=24 for solid elements and for shell elements keep Ishell=24 and N=5 in property card. This will control hourglass issue.
The error % is an energy error value. A small amount of contact energy can lead to a large % energy error. As we know that the high contact energy is caused by the friction and thus it is OK to have the energy error when you use the friction.
0 -
Thank you George,
To avoid computation time, I am trying the same with I shell=24 for both the sleeve. Only ring part is made solid Tetrahedron( No HOURGLASS). By doing so there is no hourglass issue, but run gets terminated by mass error even with no impossed DT/NODA/CST value for timestep.
Whats the reason for mass error ? How can i eleminate it
0 -
Hi Karthic,
Please send across the files (model file, engine file,starter out and engine out files)
0 -
Hi George,
File have been sent, sorry for the delay.
0 -
Hi,
You can try running the model with a lower time step. Seems like the ring component deforms more dropping the time step and ending up in the termination of the run. You can also recheck the material parameters for the ring component.
PS: If you set the friction coefficient to zero and rerun and that removes the large % energy error then you can ignore the large error happening during the run.
0 -
Thank you George, let me try.
0