How properly represent gas exit in inspire cast
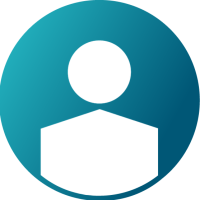
Answers
-
Dear Paulo,
I think it is a smart approach what you did with the overflows...but then you would require the system to give you at least air velocity visualization to take profit of this injection extension that you are generating with these false overflows. Air velocity isn't going to be the same you see for the metal.
In terms of model, it should be clarified from the solver developer how is the air exhaust considered. Air behaviour is for sure within the model (byphasic system), quite unique within casting solvers, let me say.
Meanhile you can get a closer look to air velocity like this:
You can check it by going to 'Results/Filling/Air Flow', label a point of mesh in the overflow gate and see the air pressure/chamber pressure. See enclosed picture for a mesh with 0,2 refining factor for overflows.
It wouldn't be unrealitstic to get this velocity info visualized in future releases. Meanwhile you can see it in the labelled points spreadsheet. (Up to 2,1m/s in label 2. Up to 3,8m/s in the last 'overflows' with air transition). We should expect higher velocities with more realistic 0,1-0,15mm thick 'false overflows'.
Remember that you have the chance to refine mesh for these overflows with a factor down to 0,2 for a detailed analyse at these 'ventings' (last step 'Analize', secondary label 'Advanced').
By the way I don't see the bottom line of modelling with two velocity steps whit a model without runner system. Basic configuration with time (0,1s?) or speed (single value 30m/s?) .
I hope my answer being hepfull. I enjoyed discovering new software capabilities.
Cumprimentos,
Òscar Íñigo
1 -
Oscar Inigo_22496 said:
Dear Paulo,
I think it is a smart approach what you did with the overflows...but then you would require the system to give you at least air velocity visualization to take profit of this injection extension that you are generating with these false overflows. Air velocity isn't going to be the same you see for the metal.
In terms of model, it should be clarified from the solver developer how is the air exhaust considered. Air behaviour is for sure within the model (byphasic system), quite unique within casting solvers, let me say.
Meanhile you can get a closer look to air velocity like this:
You can check it by going to 'Results/Filling/Air Flow', label a point of mesh in the overflow gate and see the air pressure/chamber pressure. See enclosed picture for a mesh with 0,2 refining factor for overflows.
It wouldn't be unrealitstic to get this velocity info visualized in future releases. Meanwhile you can see it in the labelled points spreadsheet. (Up to 2,1m/s in label 2. Up to 3,8m/s in the last 'overflows' with air transition). We should expect higher velocities with more realistic 0,1-0,15mm thick 'false overflows'.
Remember that you have the chance to refine mesh for these overflows with a factor down to 0,2 for a detailed analyse at these 'ventings' (last step 'Analize', secondary label 'Advanced').
By the way I don't see the bottom line of modelling with two velocity steps whit a model without runner system. Basic configuration with time (0,1s?) or speed (single value 30m/s?) .
I hope my answer being hepfull. I enjoyed discovering new software capabilities.
Cumprimentos,
Òscar Íñigo
Thank you so much Oscar for spending time with my question and for your answer! Certainly helped me a lot to understand better how study this situation in the actual version.
Once more, thank you!
Paulo Araujo
0