Telescopic landing gear modelling
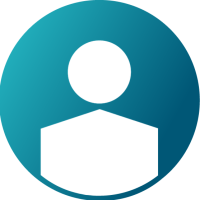
Hello this is my first question and it is about how to model correctly a telescoping landing gear with the piston moving inside the cylinder.
One bearing moves with the piston and exchange forces with the cylinder. Another bearing is at the bottom of the cylinder and exhanges forces with thr piston. As the piston moves the bearing must be applied at different relative positions.
The piston and the cylinder must be flex bodies to properly account for spin up and spring back loads. elasticity is very important in this case.
Any help? The only thing in my mind is to introduce some reference points along the axis of piston and cylinder (a serie of RBE spiders for example) and then apply a couple of PTdCV constraints.
Answers
-
Hello Luca - With what you described, it seems possible to model this with MotionView and MotionSolve. But some pictorial explanation of how bearings are connected to the piston/cylinders would help someone to give a more accurate answers.
If you can post a pic of the assembly cross section that could be helpful
Regards
Praful
0 -
yes you are right but I am still in a feasibility study, trying to understand how to. So at the moment I cant show much
The easiest way is to model the piston as a beam (it is basically a circular beam in reality). Draw on this a deformable curve and apply the constraint with the bearing placed at the bottom of the cylinder (in a similar fashion to one of the tutorial reported in motionview user guide). The point used will be the center of an RBE3 placed at the CG of the bearing, assuming to use a FE flex body with solids.
Many of these points will have to be defined along the cylinder. So the cylinder will be a serie of axial RBE3 elements. The bearing on the piston will have another point 2 curve contraint. This should correctly model the two constraints I wanted to have and correctly depict the landing gear response at landing.
0 -
Luca Cavagna_20569 said:
yes you are right but I am still in a feasibility study, trying to understand how to. So at the moment I cant show much
The easiest way is to model the piston as a beam (it is basically a circular beam in reality). Draw on this a deformable curve and apply the constraint with the bearing placed at the bottom of the cylinder (in a similar fashion to one of the tutorial reported in motionview user guide). The point used will be the center of an RBE3 placed at the CG of the bearing, assuming to use a FE flex body with solids.
Many of these points will have to be defined along the cylinder. So the cylinder will be a serie of axial RBE3 elements. The bearing on the piston will have another point 2 curve contraint. This should correctly model the two constraints I wanted to have and correctly depict the landing gear response at landing.
What you described could work. You might have to use RBE2 if using flex as RBE3 center node which is a dependent node cannot be an interface node.
Also, MotionSolve supports flex-flex contact and you may be able to use just that.
0 -
Correct. RBE3 cannot be an interface node. My plan was not to define these nodes as interface. I agree with you to go for RBE2.
I am familiar with ADAMS and VI-Grade aircraft. All my previous models were based on them. Vi-Grade has a similar force elements to model piston-cylinder bearings. They suggest using RBE2 but their reference nodes as you correctly say will not be defined as interface grid points.
0