contact interfaces settings in compression simulation
Hello, I created a compression simulation model (a cylinder between a fixed plate and a flexible plate), it has warnings(initial penetration in interface) when calculating and the calculation time increases continuously. I've read some posts and I used the check tool to fix the intersections automatically. Also, I chose interface TYPE19 between contact surfaces of plate and cylinder, I set Igap=1,Inacti=6.
I doubt maybe the mesh is not good or there are some problems in contact interface settings(there is no physical gap between plates and cylinder when modelling).
The attached files are solver decks. Could someone help me to find out the problems?
Hi,
non-linear penalty-based contact interfaces require a non-zero initial gap. Type 24 linear contact interface can be used with a zero gap. Type 19 is computationally inefficient and since there is no edge to edge issue in your model a type 7 will be more efficient.
A rigid body was put on plates so they will not affect the timestep. The model and boundary conditions are symmetric so a quarter symmetry could be used for efficiency (this will also properly constrain the cylinder in the symmetry planes- currently it is held in place only by friction).
Thank you Hyperman, the corrected model can simulate. I have some doubts. 1. In the corrected model, a rigid body is used to put 'fix' and 'imposed velocity' boundary conditions, what's the function of load collector 'displacement_spc'? 2. In interface type7 settings, slave is component cylinder, what's master interface? Because the cylinder has 2 interfaces with upper and lower plate. 3. For user comments, what's the differences between Do Not Export and Hide In Menu/Export? 4. If the interface is Type 19, I need to put a physical initial gap when modelling rather than just adjust the interface setting parameters? What confuses me is that whether there needs a physical initial gap or not.
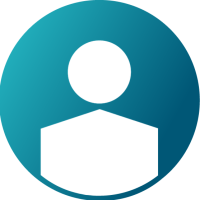
Glad to help.
1. The load collector 'displacement_spc' constrains the moving plate in all degrees of freedom except z translation. Without this constraint the plate could rotate and/or displace in unwanted directions.
2. The master segments are both plates. Usually, the stiffer component is chosen as the master. In case both components use the same material, the coarser mesh is chosen as the master.
3. I haven't used this function yet.
4. Yes, Type 7, 11, 19 need to have initial clearance (non-zero gap, Physical gap).
Hi,
non-linear penalty-based contact interfaces require a non-zero initial gap. Type 24 linear contact interface can be used with a zero gap. Type 19 is computationally inefficient and since there is no edge to edge issue in your model a type 7 will be more efficient.
A rigid body was put on plates so they will not affect the timestep. The model and boundary conditions are symmetric so a quarter symmetry could be used for efficiency (this will also properly constrain the cylinder in the symmetry planes- currently it is held in place only by friction).
Unable to find an attachment - read this blog