Problems with topological optimisation of assembly ERROR # 312
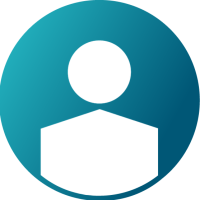
Good morning,
I am doing a topological optimisation and during the execution I found the error 312. My model is divided into 5 components, which are assembled, since it is easier for me to assign the mass fraction to each one.
Searching through blogs and old discussions on the ALTAIR platform, the recommendation was to perform a static analysis to check that the model works well and that there are no large displacement values. As a result, I got a value of 80 mm and a stress of about 400 MPa.
I rechecked the mesh, performed a modal analysis and no strange results were obtained (the first 6 modal responses were close to zero). Next, I wanted to test a model composed of a single part. What I found with this configuration was that during the static analysis the maximum displacement decreased to 27 mm and the stress to 170 MPa. Finally, the software successfully optimised this model.
So, the conclusion is that there is a problem when my model is divided into several components and assembled.
I would like to know if I should create some kind of "link" between the components in addition to the assembly. Or what should I do so that this error does not occur.
I share with you the two .fem files
Thank you in advance