[SOLVED] Timestep size for ALE Mesh + Free surface
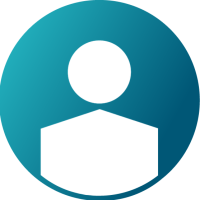
Hello everyone,
I would like to ask if there is any special requirement in order to determine the proper timestep for simulation that use ALE Mesh + Free surface. Usually, i calculate my timestep using Courant number = 0.5, but still after sometimes the simulation crash with error: Severe mesh distortion; must reduce time increment.
Is there any proper/correct formula to calculate timestep size for these condition?
*I am simulating a vibrating cylinder.
free stream velocity: X-direction
active cylinder motion: Y-direction
Answers
-
Altair Forum User said:
Hello everyone,
I would like to ask if there is any special requirement in order to determine the proper timestep for simulation that use ALE Mesh + Free surface. Usually, i calculate my timestep using Courant number = 0.5, but still after sometimes the simulation crash with error: Severe mesh distortion; must reduce time increment.
Is there any proper/correct formula to calculate timestep size for these condition?
*I am simulating a vibrating cylinder.
free stream velocity: X-direction
active cylinder motion: Y-directionIn case my simulation is unclear.
0 -
If the flow rate is high enough such that there might be a breaking wave by/around the cylinder, you'll get failure, since AcuSolve requires a constant fluid topology. Try it with a lower flow rate to see if it holds together. Generally you want 30 to 50 time steps per 'vibration' cycle, but more would be better. How well does it work without the free surface boundary condition on the top surface - just doing the riser motion?
0 -
Altair Forum User said:
If the flow rate is high enough such that there might be a breaking wave by/around the cylinder, you'll get failure, since AcuSolve requires a constant fluid topology. Try it with a lower flow rate to see if it holds together. Generally you want 30 to 50 time steps per 'vibration' cycle, but more would be better. How well does it work without the free surface boundary condition on the top surface - just doing the riser motion?
The flow rate is quite high as the reynold number is 8500. Inlet & initial condition velocity was set at 0.34 m. I still insist to include free surface technology due to validation purpose with experiment. For now, maybe i should try without the free surface (simplification).But still, are there any work around to include free surface tech in the simulation?
0 -
Does the experiment show wave breaking - or is the free/top surface fairly smooth? You may also want to try running a 'steady' case first to establish the overall flowfield, then restart to transient with the free surface motion. Are you willing/able to share the .inp file here, for a look at it?
0 -
Altair Forum User said:
Does the experiment show wave breaking - or is the free/top surface fairly smooth? You may also want to try running a 'steady' case first to establish the overall flowfield, then restart to transient with the free surface motion. Are you willing/able to share the .inp file here, for a look at it?
Yes, the experiment does show chaotic wave breaking near the free surface of the cylinder. I will try your suggestion. Another question, if the freestream velocity is at 0.34 m, what velocity should i use at initial condition? should it be the same as free stream or set it at zero and make it increasing gradually over time until it reach 0.34 m?
Unfortunately, i cannot share the .inp file. I am very sorry.0 -
I would suggest 0.34 m/s as initial conditions, and run a 'steady' state first to establish some sort of flowfield, before switching to transient and mesh motion at free surface. If you're more interested in the buildup of the wave at the cylinder, then you could start from rest and increase the velocity over time within a single transient run. That will just take longer to develop to the full behavior at the cylinder. But, again, since you say the experiment does show chaotic wave breaking, you won't get very far with the single-phase free-surface simulation, since you'll get mesh distortion. (You need a constant fluid topology, and a chaotic breaking wave is not a constant fluid topology.)
0 -
Thank you so much for your insight & advise. So i can conclude that single phase - free surface simulation does have its limitation. Multi-phase simulation cross my mind now. What do you think about multi-phase simulation? Does it consume more computational power compared to single phase - free surface or less (based on your experience if you have any)?
*For the time being, i am running the simulation without free surface (Slip).0 -
Multiphase will be quite a bit more computationally expensive - more equations, interface tracking, etc.
0