Contact simulation seems converging, then it does not converge
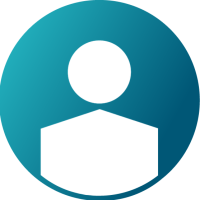
Good night dear all I hope you can help me.
I have a panel with several contact, I am working with non linear simulation (quasi static, applying an specific displacement on spc rb3 node.
My simulation seems converging quite nice but after a while (reaching 500 iterations), then the output panel displays an error of minimum iteration reached.
I increased my number of increments from 100 to 200 and the problem persists. I have the expertnl and cntstb activated also I increased the number of cutbacks and the error stills.
Most of my contacts are having mcohed material, and the parameters seem quite ok.
The simulation (the non converged) reaches up to 2.1 mm displacement, such value is actually the value obtained in the experiental characterization, hence it seems the simulation is ok, but after 2.1 more or less the simulation stops (I know there is a failure there but I would like to simulate a bit more to see how the failure progresses).
In the attached file you will find the case and the out file
Thanks in advance
Best Answer
-
Alberto CAMPUZANO said:
Dear Paul
Sorry for the late reply, yes it converges, however the displacement and force are quite different from the results obtained experimentally, however I decided to lower the k's values and the model does not converge.
During this days I've been struggling with that, because experimentally my panel reaches a maximum displacement of 2.1 mm (around) and 560 in force.
I was wondering if my problem comes from the DMGEVO or the DMGINI.
do you have any ideas?. Look I feel I already tried everything, I am getting desperate.
Thanks in advance
I am not sure what your aim is exactly to reach?. If I look at force vs disp for the modified model (with K2 and K3 set at the higher of your 2 values) and compare to one where I set K2 and K3 to the lower of the 2 values, the numbers seem close to your targets? The model with smaller values shows reduction in force toward the end (when convergence then fails, this is not unexpected if the force begins to drop like this) As I said in first email, I think maybe using true stress/strain curve may help here. But overall it seems close to your values?
0
Answers
-
There is a recommendation in help that when being used for cohesive contact K2 should = K3 in the MCOHED
In the attached I changed the K2 to match K3 and the model was able to converge (I had also set the non cohesive contacts to FINITE sliding and increased the timestep from 5e-3 to 2e-2)
One other thought, with the level of deformation it might be better to use true stress?
1 -
Dear PaulPaul Sharp_21301 said:There is a recommendation in help that when being used for cohesive contact K2 should = K3 in the MCOHED
In the attached I changed the K2 to match K3 and the model was able to converge (I had also set the non cohesive contacts to FINITE sliding and increased the timestep from 5e-3 to 2e-2)
One other thought, with the level of deformation it might be better to use true stress?
Sorry for the late reply, yes it converges, however the displacement and force are quite different from the results obtained experimentally, however I decided to lower the k's values and the model does not converge.
During this days I've been struggling with that, because experimentally my panel reaches a maximum displacement of 2.1 mm (around) and 560 in force.
I was wondering if my problem comes from the DMGEVO or the DMGINI.
do you have any ideas?. Look I feel I already tried everything, I am getting desperate.
Thanks in advance
0 -
Alberto CAMPUZANO said:
Dear Paul
Sorry for the late reply, yes it converges, however the displacement and force are quite different from the results obtained experimentally, however I decided to lower the k's values and the model does not converge.
During this days I've been struggling with that, because experimentally my panel reaches a maximum displacement of 2.1 mm (around) and 560 in force.
I was wondering if my problem comes from the DMGEVO or the DMGINI.
do you have any ideas?. Look I feel I already tried everything, I am getting desperate.
Thanks in advance
I am not sure what your aim is exactly to reach?. If I look at force vs disp for the modified model (with K2 and K3 set at the higher of your 2 values) and compare to one where I set K2 and K3 to the lower of the 2 values, the numbers seem close to your targets? The model with smaller values shows reduction in force toward the end (when convergence then fails, this is not unexpected if the force begins to drop like this) As I said in first email, I think maybe using true stress/strain curve may help here. But overall it seems close to your values?
0 -
Paul Sharp_21301 said:
There is a recommendation in help that when being used for cohesive contact K2 should = K3 in the MCOHED
In the attached I changed the K2 to match K3 and the model was able to converge (I had also set the non cohesive contacts to FINITE sliding and increased the timestep from 5e-3 to 2e-2)
One other thought, with the level of deformation it might be better to use true stress?
Good night dear Paul and sorry for the late reply
took me a while to reply, because as was looking for some delamination at 2.1 mm, doing some test and changing values.
However, because of your help adding K3 equal to K2 everything converged but the problem of delamination was not presented, then i did the whole model again, but this time i add a property PCONT with zero friction coefficient and ALLOW SEPARATION as YES.
Then, everything converged and the delamination was visible.
I thought, that using only MCOHED automatically allows separation, but that's not the case, hence the PCONT property is highly needed.
Anyways thanks you very much Paul, you helped me a lot
0