Failure in creating flexible bodies due to geometry irregularities
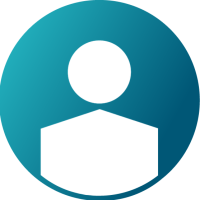
I have a two part plastic tub [front (highlighted in orange) and rear] that I want to analyze as flex bodies. I was able to process front part as a flex body but the rear part failed due to geometry irregularities. I am not sure what geometry irregularities are. How do I find what part features are failing for rear tub? Thanks.
Answers
-
Hi Raj,
I am sorry to hear about the trouble. This is an issue we have seen on a few imported CAD models and we are planning mesh quality checking and handling improvements in an upcoming release.
Currently, there is no direct way of identifying the problem elements, but you can try the following options in this order:
- Select the part. In the Property Editor, select Mesh and select Override. Enter a smaller element size. Also try a larger size.
- Visibly scan any small feature areas that are suspicious and use geometry defeaturing tools to remove the problem feature(s). You can also drag and drop the optiAnalysis.fem file right over the top of your model and this will overlay the mesh so you can visibly scan for suspicious elements, like shown here:
- If you have experience with other HyperWorks products, like HM or SimLab, there are simple techniques (not covered here) for reading the .fem and identifying these elements visibly. You can open the Run folder where the flex body files are created and view either the optiAnalysis.fem or optiAnalysis.out file and look for problems related the mesh elements, like this example of the optiAnalysis.out file where element #5551 is problematic for the given mesh size.
Element # 5551, element type TETRA. ERROR - Acceptable range violation: Face Skew Angle = 85.446 upper limit = 85.000 ERROR - Acceptable range violation: Face Vertex Angle = 2.2845 lower limit = 3.0000 *** ERROR # 2203 *** Error(s) encountered during element check ***** Element Quality Check Failed - error limits violation *****
Are you able to share the model, or at least a sub-set of it that still has the issue? These cases are good to have for development and testing (only). If you are able to share, we can take this offline and I can upload a secure FTP link. The model will be placed into a ticket with a reference number. The more case models we have showing issues, the more robust our testing can be as we work to improve the handling.
Thank you for inquiring on the Community.
Best regards,
Scott Z
0 -
Scott,
Thank you for your follow-up. Mike Johnson, Technical Director, Midwest US, is helping me as well. I will be glad to upload the model is you send FTP link.
Thanks again,
Raj
0 -
Scott,
I tried smaller mesh size as well as simplifying the geometry. That did not help. I have not tried HM. I will try to mesh it in HM. Thanks for the suggestion.
Raj
0 -
Raj Deshpande said:
Scott,
I tried smaller mesh size as well as simplifying the geometry. That did not help. I have not tried HM. I will try to mesh it in HM. Thanks for the suggestion.
Raj
Hi Raj,
Thanks for the feedback. I have sent you a request for secure file upload.
Scott Z
0 -
Scott,
After spending considerable time (trial and error method) simplifying the part, I was able to convert one of the last parts to flex bodies. However, when I import this part in an assembly it fails to covert to flex body (not an issue with other parts) . I was also able to mesh the part (in HM) without any quality issues.
Surprisingly, intricate part features had nothing to do with the flex conversion. Not sure, what criteria affects the geometry irregularities.
0