Flexible body Gear analysis
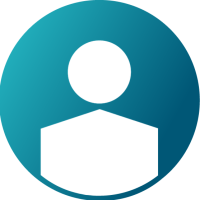
Hello,
I have just complete the course on Altair university of Multi Body Simulation and as a practice I am trying analyze the stress distribution on coupled gears. I want to provide angular velocity to one gear and analyze the stress.
I did create the flexible bodies , contact and motion but i had an error!
Contact graphics undefined for contact force id = 301001!
I believe its because i create a rigid to rigid contact between the bodies, later i created the deformable surface and set the contact(Point to deformable surface) but the simulation isnt what i was expecting.
Can you tell correct way to analyze the problem? Which step have a gone Wrong?
Answers
-
Please check out our examples library at:
https://altairhyperworks.com/motionsolve-models/
Example MV08 is something pretty close to what you are trying to do, I think. This is a non-trivial problem, especially for a new user, so hopefully the example model will provide you with the right guidance.
0 -
Thanks @Chris Coker for your reply!
Its been 2 days and my Altair Connect account is not yet approved.
Can i get those files anywhere else? I need them urgently.
And also,
Can we create a contact between two flexible bodies??
0 -
The 3d contact does not support flexible bodies. There are some workarounds for this, but they are complicated, and not typically recommended.
I'm sorry you are unable to access Altair Connect. I would recommend you reach out to your local Altair office where they can resolve that issue for you.
0 -
One more comment, you have tagged 'MotionView 13' in your post. I would highly suggest upgrading to the latest version of Hyperworks. If you are really using verson 13, you will find that our contact implementation has improved significantly. I would not recommend using contacts with versions prior to version 14.
0 -
Thank You for your valuable response!
I can have done my course fully and covered and practice all the problems ,but it seems that there is lot to discover more in motionview.
Is there any other resource or any other tutorials that can help me.
And also certain contact i make with right stiffness and exponent , while animating the bodies seems to be intersecting each other.
What may be the case?
0 -
The example models library that I listed previously is our main repository for demo models. These models also include step-by-step instructions. They should be your next resource.
We also offer additional training classes, beyond the Intro to MotionView class (assuming you have already attended one of these).
Please review the section in our help 'Best practices for contact modeling' it gives a lot of details. There are many ways you can make mistakes when modeling contacts, based on your limited description it's impossible to really give you useful advice. Contacts in general are non-trivial, and for a new user I expect you will have an initial steep learning curve. We are here to help, though.
If you can provide a sample model that replicates the behavior you are experiencing, we can take a look.
In general though, the stiffness and exponent are increased to minimize penetration between parts. I would not use an exponent more than 2.1.
Sometimes, changing the normal load calculation from Impact, to Poisson, or Volume method can help.
You may also need to go to the Advanced Settings, and turn on the feature 'find precise contact'. Also make sure in your simulation settings, you are using a max step size no larger than 1e-3. Sometimes, depending on the problem 1e-4 is a better starting point. Again, all of these technique are covered in our 'best practices' for contacts.
0 -
Here I have attached a demo file of which I am trying to analyze the forces ad stress.
Animation seems to be fine but the force graph plotted is ranging from 0 to 6E+007 which I think is problematic...
Can you help me getting right force analyzed for the model.
0 -
Hi Chinmay-
Unfortunately, you did not include the .h3d graphics associated with the gears, so I am really unable to run your model.
However, looking at the contact settings, and integrator settings, it's clear you have not followed the advice I provided in my previous post. You cannot just use the default values and expect acceptable results when dealing with contacts.
Please work through tutorial MV-1010 carefully as it will show you a good workflow and a good starting point for integrator settings.
You can also search the help for terms 'Best Practices 3d Contacts MotionSolve' and that will provide you with many details and hints on good contact simulation. If you have Altair connect access, I'll post the link below:
Chris
0 -
Sorry to disappoint i could not get access to Altair Connect that's why i could not read those guidelines, I have contacted Altair connect and hope they will grant me access.
After going through those tutorials and guidelines , I will surely re-upload my files.
Thank you.
0 -
Note that the tutorial MV-1010 should be included with the software installation. This will give you a good place to start, and Altair Connect access isn't required.
For starters, reference my comments from Thursday:
'You may also need to go to the Advanced Settings, and turn on the feature 'find precise contact'. Also make sure in your simulation settings, you are using a max step size no larger than 1e-3. Sometimes, depending on the problem 1e-4 is a better starting point. '
In the future, when sharing models, use File -> Export -> Model, and select the option 'Archive' in the dialog box that opens. This will create an archive not only of your .mdl file, but any externally referenced files. This will ensure that any files need to load and run the model are included.
Chris
0 -
Chris Coker_21312 said:
Please check out our examples library at:
https://altairhyperworks.com/motionsolve-models/
Example MV08 is something pretty close to what you are trying to do, I think. This is a non-trivial problem, especially for a new user, so hopefully the example model will provide you with the right guidance.
Hi,
Our Client problem statement is also the same, the above mentioned link is not working.
Please guide us to get the same model for better understanding.
Regards
Pranav Chauhan
DesignTech Systems Pvt. Ltd.
0