HyperCrash Seat Foam Zero or Negative volume for 3D element
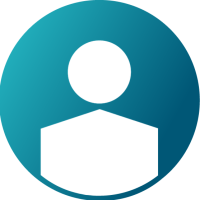
Hello,
I'm trying to run a dummy seat crash similar to tutorial RD-3150 except my simulation keeps crashing because of this error. I'm using Radioss Block 140, and FOAM_PLAS is the material being used.
Basically what is happening is the seat foam starts imploding and then rapidly explodes. Clearly, the seat foam is getting deformed so severely that the it ends up becoming a negative volume. It may also be important to note that this failure does not always occur, only sometimes.
I'm wondering why this didn't occur in the tutorial and also wondering how I can fix it?
Should I assign a failure criterion to the foam elements so they start getting deleted at higher strains?
I've seen similar forum posts on this error and the solution has been to change strain formulation settings but I am not too familiar with these.
Thanks.
Answers
-
FOAM_PLAS material is the one being used
0 -
Hi @kjc95
Please see this FAQ from RADIOSS help:
I used solid elements and the run stopped before the end time, with the message: 'Zero or Negative Volume': How can this problem be solved?
This happens when solid elements are very deformed and their characteristic length goes to 0. You may notice in the output file before getting this error message, the time step of the element written into the message drops down.
In case of large strain formulation, the time step of an element goes to 0 when the element is compressed. In a mathematical way, the element cannot reverse its orientation since its stiffness increases to an infinite value; but due to numerical accuracy, the element may go to reverse its orientation.In order to solve the problem of both the drop in cycle time step and subsequent termination of the run due to a negative volume, you might first check that the material used is well-suited to the physics which is represented. Then switch the elements to small strain formulation. This is done as follows:
In the RADIOSS Starter input file (Runname_0000.rad), use Ismstr =2 in the solid property or in the option /DEF_SOLID; in RADIOSS Engine file (Runname_0001.rad) use the option /DT/BRICK/CST which will set the time step value
at which the solid elements will switch to small strain.
This means that the solid elements using Ismstr =2 will use large strain formulation while their time step remains greater than
, and will then switch to small strain formulation.
Their volume will then remain constant and the element can even reverse its orientation. The drop of their time step normally stops except for some materials, especially viscous materials.
0