Heat transfer coefficient
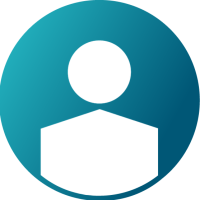
Hello guys,
I got a question how to plot surface film coefficient distribution in case where all BCs are wall type with defined temperature values only and fluid is treated as static. I know that turbulent model has to be selected but still I am getting zero values.. Is therea way to omit neccessity of defining inflow or outflow?
<?xml version="1.0" encoding="UTF-8"?>
Answers
-
The surface film coefficient depends on having velocity gradients (non-zero wall shear) in a turbulent flow solution. With all zero velocity values, the surface film coefficient will also be zero.
For a general heat transfer coefficient in a case like this, you'll probably need to use your own reference temperature and use:
HTC = Q / ( T_ref - T_wall )
Q == local surface heat flux - For that, you'll need to use a non-zero value for surface nodal output, rather than just integrated output
T_ref == your specified reference temperature
T_wall == the local wall temperature0 -
so in order to get surface heat flux I should just put 1 next to Nodal time step frequency (see attachement)?
But what if I would like to get the heat flux value measured from one end of the tube to the other (assuming 1D conduction case)? Should I first average the inlet and outlet surface heat flux values and then calculate the arithmetic mean?
0 -
If it's a steady-state calculation, you can just set 'Nodal time step frequency' to 1000 - so it's written when you get the clean stop of the job. You don't need it every time step. (You can, however, leave 'Integrated time step frequency' at 1, so you get the integrated values each time step to track convergence.)
If it's 1D conduction, insulated at the walls, you should have the same integrated heat flux value at the inlet and outlet, but with opposite signs, as at steady state the energy must balance.
0 -
thanks for your reply!
But what if I have surface heat flux distributed as on the attached picture? Distribution in that case is not uniform due to another medium inside the domain filling out the gap between two solids in contact
All other walls are insulators and heat travels in one direction only. How to get average value of heat flux to get the heat transfer coefficient across the medium?
0 -
ok, problem solved. I integrated surfaces in AcuField.
Thanks again.
0 -
You can also get the integrated heat flux directly on those surfaces from acuTrans / acuProbe. This will also then be consistent with the AcuSolve formulation where the integrations in AcuFieldView will be slightly different.
0