How to perform Kinematic and Dynamic analysis of a Sprocket-Chain Conveyor using MotionSolve\MotionView?
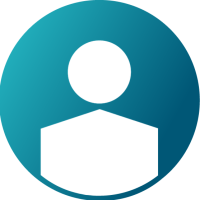
I need to perform Kinematic and dynamic analysis of a Non-Circular Sprocket Chain Conveyor system using MotionSolve\MotionView. The system consist of a driving sprocket, an idler sprocket, a non-circular idler sprocket and conveyor chain as shown in rough figure of cross-section of conveyor belt. The conveyor is slacking on lower span, as the conveyor is sufficiently large for non circular sprocket to move at all conditions. The conveyor moves with a periodic to and fro motion between two extreme positions related to non-circular sprocket(elliptical pitch curve) orientation.
A real life example of such sprocket-chain conveyor
There are following things that I wanted to know as I am new on this platform and I will be really grateful for the related guidance given to me.
- Is there a dedicated module(or wizard) to model a Sprocket Chain Drive\Conveyor in MotionSolve\MotionView or any altair software?
- What must be the Constraints(or joints) and inputs that I must use for simulation and analysis of the Chain Conveyor?
- Is there a dedicated module for modelling a Non-Circular Sprocket in any altair software?
- Am I using the correct software and procedure for solving the stated problem?
Thank you for your reply.
Answers
-
Hello Raj -
There are few different ways to model and solve a chain drive with Altair's motion solutions.
A. MotionView
From version 2021, there is a Track builder tool that can be accessed from the Model menu
It is mainly aimed at building tracked system, but the tool can also be used to build chain drive as the system is very similar. The tool takes you through various stages of building the sprocket-chain drive. First create the rolling system (sprocket in your case) and then create track (chain).
This tool can create chain drive system using analytical geometry such as spheres and cylinders which can solve faster due to analytical shapes. There is an option to provide CAD for both sprocket and links and use it for contacts too. In this case the solution could take more time.
I see there are cross links connecting the chains. This would have to be added manually and attached to each of the link body. For 100s of links this will be quite cumbersome through the GUI. Hand editing the model file using a text editor is a faster approach.
B. Inspire
Altair/Inspire has motion capabilities that work with geometry directly. A CAD model of the entire chain assembly can be imported into Inspire. It has abilities to find joints for the assembly and can create hundreds of joints as in case of chain drives very quickly. Setting up contacts in bulk is also easy and fast.
There is no need to adding the cross links separately (if they are part of the CAD assembly) and Inspire can identify joints automatically.
Note that this is an analysis with 3D contacts between chain and sprocket, so the solution could take more time.
Hope this helps.
Feel free to contact us again if you need more assistance.
Regards
Praful
P.S Sorry for the very late reply. the original post was in a different forum.
0