XFEM in M27_plas_brit - crack without deletion?
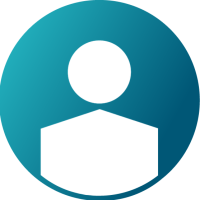
Answers
-
Hi,
Can you try with Ixfem=1 in /FAIL/FLD card?. If XFEM flag is activated (Ixfem=1), the failure criteria will lead to element cracking instead of element or layer deletion.
You can also go through a webinar on stone impact simulation at http://www.altairuniversity.com/conceptual-design-of-a-3-wheeler-motorbike/conceptual-design-of-a-3-wheeler-motorbike-stone-impact-simulation/
0 -
Hi George,
both Xfem=1 and Xfem=0 give the same result - always part of elements is gone.
I'll watch webinar and answer later whether I found solution or not.
Thanks,
Piotr
0 -
Hey,
please correct me if I'm wrong, but on the postprocess video I can see similar issue - some of splitted elements has been removed during solving.
I am using the same sandwich property and mat law 27, but with thin polymer (without fail) film between two glass sheets.
In a postprocess you can watch at each layer separately, so let's look at upper glass sheet. I can't understand one thing - why element is first cracked and after few time steps cracked parts are removed, while there is no high strain on them since they are already cracked?
Can someone help me to understand and, what is more important, avoid the deletion?
Thanks,
Piotr
0 -
Hi,
It is possible to control the crack propagation using XFEM methods in RADIOSS. But the user should be well aware about the damage parameters of the model. If the user has the exact damage parameters it is possible control the cracking without deletion of the element provided user has control over loading.
But in cases cases like impact or drop it is very tough. We cannot predict the impact/shock happening in the model and so we cannot control the crack propagation. In such cases we cannot avoid element deletion during crack propagation.
0 -
Hi George,
I'm currently dealing with a similar simulation. I modeled a laminated glass shell using P11 SANDWICH in order to simulate an impact between a human head and an automotive windscreen.
The sandwich is composed by three layers, glass-PVB-glass. I choose M27 PLAS BRIT to model the glass and i used the FAIL FLD card as suggested in the webinar on stone impact simulation at http://www.altairuniversity.com/conceptual-design-of-a-3-wheeler-motorbike/conceptual-design-of-a-3-wheeler-motorbike-stone-impact-simulation.
<?xml version="1.0" encoding="UTF-8"?>
Unfortunately few elements of the upper glass layer after cracking are completely free (because the adjacent were deleted) and start to stretch the PVB layer (which is not supposed to break, so basically is just stretched by this free moving elements).
The simulation is quite good in general (I mean the head-form acceleration values are ok, and the contact forces as well), but, observing the animation, is quite unreasonable that the PVB is deforming in this way.
Do you have any suggestion to solve this problem?
It's kind of urgent, I'd really appreciate any help.
Thanks in advance!
Ilaria
0 -
Hi,
Can you check the element deletion criteria?
0