Liquid expansion inside Container
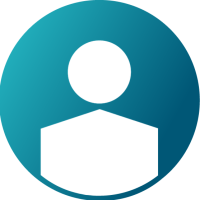
I have created the model of a closed container (cuboid) and inside this container is a liquid that expands due to thermal loading (temperatures). The expansion then induces stress in the container walls.
For the Container I have created a 2D Shell Mesh and for the liquid a detached 3D Hexa Mesh of the same size (fully filled container). Then I created contacts between the nodes of the liquid mesh and the elements of each surface so that it is kept inside the container and creates pressure.
My question is now how do I define the matrerial properties of the liquid inside the container correctly and did I define the contacts correctly?
I could not find any options to define a liquid with the thermal expansion coefficient. So far I have defined it as a MAT1 PSOLID Material (with the bulk modulus as e modulus):
[System: mm-t-s]
This how I created the contacts (overall 6 contact definitions, one for each surface):
But solving it like that leads to high stresses (in picture T = 300K, so only increased by 6,85K compared to TREF) and also the displacement shows that the Liquid (blue in picture) expands more than the surfaces (so its not inside anymore).
I would appreciate if anyone could help with these problems or has ideas how to solve them.
Answers
-
your setup looks ok to me. SLIDE Contact in linear analysis should be fine. Maybe you could force CLEARANCE=0.0 to make sure the contacts are already closed in the first place. But other than that, it looks ok to me. For the liquid, yes, you will need to model it as a "soft solid".
0 -
Adriano A. Koga_21884 said:
your setup looks ok to me. SLIDE Contact in linear analysis should be fine. Maybe you could force CLEARANCE=0.0 to make sure the contacts are already closed in the first place. But other than that, it looks ok to me. For the liquid, yes, you will need to model it as a "soft solid".
When I force CLEARANCE=0.0 it appears to improve the Displacement result a little but still the liquid expands more than the surfaces.
Is there any reference on how to choose the material parameters of the "soft solid" so that it is comparable to the behaviour of a liquid?
Putting the bulk modulus as e modulus seems physically incorrect.
Or is there maybe a different software with which I can simulate a case like mine?
0 -
HGH said:
When I force CLEARANCE=0.0 it appears to improve the Displacement result a little but still the liquid expands more than the surfaces.
Is there any reference on how to choose the material parameters of the "soft solid" so that it is comparable to the behaviour of a liquid?
Putting the bulk modulus as e modulus seems physically incorrect.
Or is there maybe a different software with which I can simulate a case like mine?
under your contact options, you could try changing the discretization to S2S (surface-to-Surface), so that the contact more distributed.
I don't know for sure how to measure the effective equivalent modulus, as well.
0 -
Adriano A. Koga_21884 said:
under your contact options, you could try changing the discretization to S2S (surface-to-Surface), so that the contact more distributed.
I don't know for sure how to measure the effective equivalent modulus, as well.
I tried that but it did not make any difference in the results.
0