Issues with defining Gap/Gapmin Type 7 and Type 2.
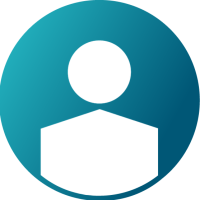
Hey Altair and Radioss Community,
I think I have solved my problem myself, but just to make sure I am correct. I want to simulate a tube crush and the tube is attached to a rigid surface at the top and bottom (picture). I have attached the tube to the surface with type 2 interface.
- To make the internal contact, I set up a type 7 interface with the tube and surface as the master and slave elements. Since the smallest element side length of the tube is much smaller than the surface thickness, the gap was smaller than half the thickness of the surface. As a result, I saw that the tube was penetrating the surface.
- To eliminate the problem, I set up 2 Type 7 interfaces, where:
- one only for the tube itself (master and slave element) with a gapmin of the smallest element length of the tube.
- The other interface was for the contact between the tube and the surface (main layer and slave tube). As Gapmin half the thickness of the surface
So I cant just simulate the surfaces as they are without regarding the thickness as I read everywhere. Am I right?
Best regards
Leopold
Answers
-
Sort of, it depends, which settings you use for igap and iremgap
With default igap (1000) gapmin is the contact thickness, and your approach would work, but normally it is better to use an automatic thickness (igap =1,2 or 3)
I usually use igap = 2 and iremgap = 2 you should set a small gapmin (e.g. 0.5mm) the contact thickness will be calculated automatically and self penetrating nodes (where element edge length is less than thickness) will be neglected by neighbouring elements
For the end connections, if they are rigid, you may include the ends in the rbody instead of using type 2, if the end of the beam is too close for the contact with the plate in a type 7, then it is simplest to just move it away, but your approach of having a manual thickness TYPE7 with a smaller gapmin is ok too.
If you want to take care of it all automatically in one contact without moving your end plates or beam ends, there is another way still...you can set igap =2, iremgap =2, set a small gapmin and set thickness on the PART card (for contact thickness only) of your end plate to a value lower than it's actual thickness
0 -
Paul Sharp_21301 said:
Sort of, it depends, which settings you use for igap and iremgap
With default igap (1000) gapmin is the contact thickness, and your approach would work, but normally it is better to use an automatic thickness (igap =1,2 or 3)
I usually use igap = 2 and iremgap = 2 you should set a small gapmin (e.g. 0.5mm) the contact thickness will be calculated automatically and self penetrating nodes (where element edge length is less than thickness) will be neglected by neighbouring elements
For the end connections, if they are rigid, you may include the ends in the rbody instead of using type 2, if the end of the beam is too close for the contact with the plate in a type 7, then it is simplest to just move it away, but your approach of having a manual thickness TYPE7 with a smaller gapmin is ok too.
If you want to take care of it all automatically in one contact without moving your end plates or beam ends, there is another way still...you can set igap =2, iremgap =2, set a small gapmin and set thickness on the PART card (for contact thickness only) of your end plate to a value lower than it's actual thickness
Thanks a lot for the explainations Paul but I've got some isses.
Can you precise what contacts you mean? Because if I set igap = 2 and iremgap = 2, either there I get inital penetration problems or WARNING ID : 477. I will share you my 0000.rad file.
Another question:
I already searched and didn't find a quick way, but is it possible to visualize the thickness of shell elements in hypermesh as it is possible in hypermesh?
0 -
The igap=2 iremgap=2 is my recommendation for the self contact
For TYPE7, the segment extends around the end of the shell, this means where you have a free face perpendicular to another, you get an artificial initial penetration, this is why you get penetrations between the crushing plates and layers if the gap is auto calculated (since the sinusoidal and plate are 1mm thick but there is only a 0.5mm gap between them)
So For the Crushing-Layer contact which is the one giving you issues still, I would either just use igap=1000 and gapmin 0.5 in this case
(this is what I meant in my first reply when I said 'if the end of the beam is too close for the contact with the plate in a type 7, then it is simplest to just move it away, but your approach of having a manual thickness TYPE7 with a smaller gapmin is ok too')
0