Convective coefficient of cooling channel
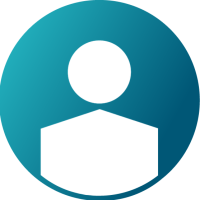
Hello experts,
I have a doubt regarding calculating calculating htc (h = Q/(a* (T_wall - T_reference))
In a cooling channel how to to determine the T_reference, is it supposed to be volume averaged temperature (Temperature in Integrated element output)?
Thank you.
Answers
-
You would want to use the definition consistent with whatever else you're doing with the information - as there could be many choices for the reference temperature. The Programs Reference Manual section for the acuTherm command gives some options. You'll likely want to review the sections with equation2 (where the user defines the reference temperature) and equation3 (where the reference temperature is taken from a given Y+ distance from the wall).
But, yes, you certainly could use integrated element output as the user given temperature. Just be sure to document what you've used, and be consistent in your approach. It all depends on what you want to compare or do with the data/results.
0 -
acupro_21778 said:
You would want to use the definition consistent with whatever else you're doing with the information - as there could be many choices for the reference temperature. The Programs Reference Manual section for the acuTherm command gives some options. You'll likely want to review the sections with equation2 (where the user defines the reference temperature) and equation3 (where the reference temperature is taken from a given Y+ distance from the wall).
But, yes, you certainly could use integrated element output as the user given temperature. Just be sure to document what you've used, and be consistent in your approach. It all depends on what you want to compare or do with the data/results.
I want to use it has an input (convective coefficient with reference temperature) for thermal analysis in OptiStruct. So which kind of reference temperature is ideal to use?
Thank you.0 -
Jagan_21383 said:
I want to use it has an input (convective coefficient with reference temperature) for thermal analysis in OptiStruct. So which kind of reference temperature is ideal to use?
Thank you.I would guess the most appropriate would be a single user-defined temperature. That way in OptiStruct you would have the heat transfer coefficient from AcuSolve, and you would define that single reference temperature.
I'm not sure what other options are there for OptiStruct - but that is probably the simplest.1 -
acupro_21778 said:
I would guess the most appropriate would be a single user-defined temperature. That way in OptiStruct you would have the heat transfer coefficient from AcuSolve, and you would define that single reference temperature.
I'm not sure what other options are there for OptiStruct - but that is probably the simplest.Thanks for your replies.
Could you please elaborate how surface film coefficient in surface outputs is computed?
And if the reference temperature is taken from a given Y+ distance from the wall, then it varies first layer height of mesh?
0 -
Jagan_21383 said:
Thanks for your replies.
Could you please elaborate how surface film coefficient in surface outputs is computed?
And if the reference temperature is taken from a given Y+ distance from the wall, then it varies first layer height of mesh?
From that acuTherm page referenced earlier - Equation 1 defines T+ as a function of Y+, using L and Beta - also defined as functions of local Prandtl number and Y+. The equation for local Prandtl number is also there - as a function of material properties: viscosity, specific heat, and thermal conductivity.
The default used for the commonly reported surface-film-coefficient is Y+ = 100. This Y+ 'location' can be modified in the TURBULENCE_MODEL_PARAMETERS command - as the value for film_coefficient_yplus
That determination of where Y+ happens for each wall node is not restricted just to where the first node of the mesh lies. It would have some dependency as the first node determines the accuracy of the wall shear stress used in the equations.
0