I have a case where I want to constrain all dof's except one rotational dof ,because ther is a bearing there ,but on doing so the stress flow stops at this point which in reality it shouldn't.
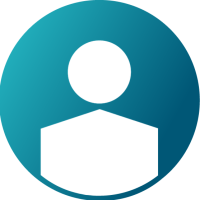
Best Answer
-
SHRIKAR WADADARE said:
Thank you very much.
Ok, simple model attached in fem format the large end is fully constrained, the 'bearing surface' has all of its nodes 'assigned displacement' in a cylindrical coordinate system defined with its 'z' (axial) direction down the centre of the part. There are SPC constraints on those same nodes, that because the nodes are assigned to cylindrical system, use that system (constrained in X for Radial, Z for axial, but free in 'Y' for tangential). The small end has an RBE2 defined on it. There are 2 loadcases, 1st is torsion case (moment defined at independent node of the RBE2), the 2nd is a bending case (load applied at independent node of RBE2)
Torsion:
Bending:
Nodes assigned cylindrical displacement system (and Y SPC constraint):
You can see the effect below, in torsion case the bearing surface allows the part to rotate and the disp/stress contours continue past it, in the bending case, the bearing constrains the displacement and creates a stress concentration (I have constrained the 'Z' direction in the bearing SPCs too, you could release that, if you wanted to allow axial movement through the bearing.
Displacement for the 2 cases:
Stress for the 2 cases:
I have used quite large loads so the movement is visible in post. In reality if rotation is significant, (0.5º +) then you should probably run as large displacement rather than small displacement.
Hope this helps, ask more if you need to!
0
Answers
-
Can you show your mesh? If you constrain 5 of 6 DOFs then it will stop stress flow to a large degree, is this for a linear or non-linear solver? Large or Small displacement?
0 -
dof's 3 and 6 unlocked
0 -
SHRIKAR WADADARE said:
dof's 3 and 6 unlocked
I think you are misunderstanding the SPC behaviour:
1st: For solid (or tetra) elements in any case there are no rotational DOF (so releasing DOF 6 is not making any difference they are already unconstrained even if a DOF 456 is set)
2nd: when you release the DOF it is at each node individually, so if your intention is to allow that whole mesh to rotate about global Z, this is not how you would do that anyway, i.e. releasing DOF 6 would not allow the whole section to rotate, the global rotation of the section is constrained by the local X and Y (1 and 2) DOFS at those nodes. All you have done is released the section to compress/extend in Z (if the loading is torsional, this would explain why stress flow ends there as the section is still constrained from rotating)
If you want to represent a bearing condition on that face, I think you should use a cylindrical coordinate system for the nodes and release the tangential direction (Y), or you could create a mesh representing the bearing surface and use a contact definition instead
1 -
Paul Sharp_21301 said:
I think you are misunderstanding the SPC behaviour:
1st: For solid (or tetra) elements in any case there are no rotational DOF (so releasing DOF 6 is not making any difference they are already unconstrained even if a DOF 456 is set)
2nd: when you release the DOF it is at each node individually, so if your intention is to allow that whole mesh to rotate about global Z, this is not how you would do that anyway, i.e. releasing DOF 6 would not allow the whole section to rotate, the global rotation of the section is constrained by the local X and Y (1 and 2) DOFS at those nodes. All you have done is released the section to compress/extend in Z (if the loading is torsional, this would explain why stress flow ends there as the section is still constrained from rotating)
If you want to represent a bearing condition on that face, I think you should use a cylindrical coordinate system for the nodes and release the tangential direction (Y), or you could create a mesh representing the bearing surface and use a contact definition instead
Thank you,
I am new to this ,so can you provide some references for creating cylindrical coordinate systems or simulating bearing contacts .
0 -
SHRIKAR WADADARE said:
Thank you,
I am new to this ,so can you provide some references for creating cylindrical coordinate systems or simulating bearing contacts .
Not to hand, I'll make a small proof of concept model and get back to you!
1 -
Thank you very much.Paul Sharp_21301 said:Not to hand, I'll make a small proof of concept model and get back to you!
0 -
SHRIKAR WADADARE said:
Thank you very much.
Ok, simple model attached in fem format the large end is fully constrained, the 'bearing surface' has all of its nodes 'assigned displacement' in a cylindrical coordinate system defined with its 'z' (axial) direction down the centre of the part. There are SPC constraints on those same nodes, that because the nodes are assigned to cylindrical system, use that system (constrained in X for Radial, Z for axial, but free in 'Y' for tangential). The small end has an RBE2 defined on it. There are 2 loadcases, 1st is torsion case (moment defined at independent node of the RBE2), the 2nd is a bending case (load applied at independent node of RBE2)
Torsion:
Bending:
Nodes assigned cylindrical displacement system (and Y SPC constraint):
You can see the effect below, in torsion case the bearing surface allows the part to rotate and the disp/stress contours continue past it, in the bending case, the bearing constrains the displacement and creates a stress concentration (I have constrained the 'Z' direction in the bearing SPCs too, you could release that, if you wanted to allow axial movement through the bearing.
Displacement for the 2 cases:
Stress for the 2 cases:
I have used quite large loads so the movement is visible in post. In reality if rotation is significant, (0.5º +) then you should probably run as large displacement rather than small displacement.
Hope this helps, ask more if you need to!
0