ERROR ID : 760
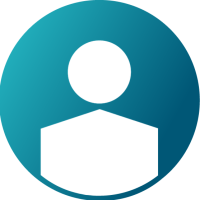
Hi guys,
I have this error with this model of a composite impact attenuator. Could you help me? I'm desperate.
Thank you for attention
Answers
-
Hi,
review and debug models using tools>Modelchecker>Radiossblock and starter out file.
ERROR ID : 266
INPUT VERSION 2018 IS NOT SUPPORTEDselect user profile 2017, because for an unknown reason 2018 is not supported.
There are problems with contacts- type 7 and 2 require initial gap so some parts ware offset, and some other parameters were defined.
I suggest connecting parts of crash-box assembly with mesh connectivity (matching) instead of using type 2 or 7 contacts.
There were also issues with composite orientation.
here is the manual option:
and here is Drape Estimator:
Drape Estimator - Altair University
You should also reduce the model, as my computer would run this simulation for the next 2 months nonstop- imagine the desperation
/emoticons/default_biggrin.png' srcset='/emoticons/biggrin@2x.png 2x' title=':D' width='20' />
0 -
Thank you @Ivan for your answer, I have copied your model to understand my errors. I copied the contact card values and modified the initial gap translating the components in the right position as you did. Your simulation run, my not
/emoticons/default_sad.png' srcset='/emoticons/sad@2x.png 2x' title=':(' width='20' />
Did you modify only these values or other too? I don't understand what composite orientation and the drape estimator is for.
Thanks for always answering me
0 -
I do not remember all the modifications I made, but it will be a good practice for you to find and correct mistakes- the error is probably due to initial penetration in type 7 interface or due to nodes not found in type 2 interface. Use the above-mentioned (model checker, out files) methods to debug models. It is an important skill to master so you will be able to correct the models yourself.
Composite orientation and the drape estimator tools are used to define element orientation. Each element has its own orientation and if anisotropic materials are used (like UniDirectional or woven composites) it is essential to establish proper element orientation. Note that angle defined for plies are in relation to element orientation i.e. plies are rotated by that angle.
0 -
Thank you again. I made a very large mesh and the time for simulation is 13 hours
. There is an alternative method to reduce time simulation? Because an advance mass scaling isn't recommended for crash simulation.
0 -
Connecting parts of crash-box assembly with mesh connectivity instead of using type 2 or 7 contacts would greatly reduce the computation time.
Traditional mass scaling /DT/NODA/CST) can be used. AMS can also be used for crash simulations, but it should be compared against CST run for validity. AMS is strictly not recommended only for high-speed events like blast and ballistics.
You can find elements/nodes/interfaces contributing to low timestep during simulation in the engine out file (runname_001.rad) or in the starter out file (runname_000.rad) search for NODAL TIME STEP (estimation). Element check can also be performed in HM using tools>check elem>time (or F10) where minimum timestep criteria can be defined and failing elements highlighted. Mesh should be finer where more deformation is expected (close to impactor).
0