ERROR ID : 257
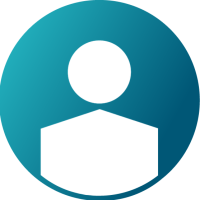
Hi,
I make this 3 point bending model but when I launch the simulation I have this error.
ERROR ID : 257
** ERROR TH GROUP
WARNING ID : 312
** INCOMPATIBLE KINEMATIC CONDITIONS IN MODEL
DESCRIPTION :
420 INCOMPATIBLE KINEMATIC CONDITIONS IN MODEL
.. GEOMETRY PLOT FILE
.. ERROR ==> NO RESTART FILE
ERROR TERMINATION
Sorry if this is my umpteenth post but I don't know who to turn to. Thank you for attention
Answers
-
Hi Antonio,
there are so many modeling errors I suggest you check the Radioss free ebook. Also please go through the attached tutorial on how to create a 3 point bend test.
For model debugging use Tools>Model Checker>RadiossBlock and review the .out files for errors and warnings.
I have modified the model so it can run:
-contact was not defined properly
-shell elements that come into contact had wrong normals orientation 2D>composites>element normals>reverse
-the plies were not referencing elements
-the laminates were missing
-delete the ^tempCompSurfSegment component
-delete the type 2 tied interface as equivalencing nodes (shift+F3) works better to connect face sheets to honeycomb
-delete the RBE3 component and use RBE2 to create rigid on stamp component
-create boundary condition on the independent node of RBE2 to block all DOF except Y translation
-edit the TH group, as it is referencing non-existing component ID 7
-the mass scaling is imposing one magnitude lower timestep (7e-7) than natural (6e-6). Instead, mass scaling should be used to impose a higher timestep.
-time scaling is recommended as 420 seconds is inefficient for explicit. Reduce the simulation duration until you get a quasi-static solution (total kinetic energy to the total internal energy is small enough - normally less than 5%).
0 -
Thank you for your answer, the model works but I have problem because the simulation continue for too time. The problem is the fail card (hashin) that check all the elements, how can I reduce this time?
0 -
I imposed 420 seconds because the test that I will realize has 1mm/min of velocity of the stamp, in fact after 420 seconds the stamp should move 7mm, that is the failure of the first ply with this configuration. But in this way the simulation time is too long. Is there a solution to abbreviate the simulation time?
0 -
Altair Forum User said:
I imposed 420 seconds because the test that I will realize has 1mm/min of velocity of the stamp, in fact after 420 seconds the stamp should move 7mm, that is the failure of the first ply with this configuration. But in this way the simulation time is too long. Is there a solution to abbreviate the simulation time?
Increase CPU power?
or
coarsen mesh where it is not really important?
or
Increase time increment by using advanced mass scaling
or
Recalculate height of punch and calculate new velocity and change the event time accordingly.
0 -
Expanding on @Prakash Pagadala's last suggestions:
You can simulate a static loading more computationally efficient by time scaling, which means applying the load more quickly than in the quasi-static experiment in order to reduce the simulation time. However, the kinetic energy should be low (5-10%) compared to the internal energy for most of the simulation, to minimize the inertial effects. You can check the energy fraction in Hypergraph by plotting both energies and using Vehicle safety tools (File-Load-Preference File) to divide curves (Math-Two Curves-Divide w/Zero).
0 -
Thank you for your help and your advices.
Best wishes
0 -
Altair Forum User said:
Expanding on @Prakash Pagadala's last suggestions:
You can simulate a static loading more computationally efficient by time scaling, which means applying the load more quickly than in the quasi-static experiment in order to reduce the simulation time. However, the kinetic energy should be low (5-10%) compared to the internal energy for most of the simulation, to minimize the inertial effects. You can check the energy fraction in Hypergraph by plotting both energies and using Vehicle safety tools (File-Load-Preference File) to divide curves (Math-Two Curves-Divide w/Zero).
Hi Ivan, how could I graph these energies? In hypergraph I haven't these variables to graph. Moreover I don't see the damage of the layers in the post process also if I have defined the Hashin card property for failure (I have hyperworks 14). Thank you for attention
0 -
Hi,
you can plot kinetic, internal, contact, hourglass and total energy in Hypergraph. Those variables are output by default and can be loaded in HG (file: runname_T01)>Global Variables>Y requests>MAG to plot.
Any particular reason for joining upper and lower face sheets to honeycomb with tied contact instead of just equivalencing nodes? Note that tied contact with spotflag=1 adds mass to the model (DM/M in the engine out file) which changes the problem physically.
To postprocess damage activate /ANIM/SHELL/DAMA output request. I have also applied advanced mass scaling (AMS and DT/AMS cards) for computational efficiency.
0 -
Thanks Ivan. I have hypermesh 14 so I cannot open your model. Moreover there isn't the engine card /ANIM/SHELL/DAMA but only /ANIM/SHELL, I don't know if you know another method to see the composite damage. I haven't particular reason, it is the only way to jain the face that I found because when you talk about 'equivalencing nodes' I don't understand what you want to say me. Sorry but I'm new with radioss and your help it's very important. Thank you again
0 -
The solver deck is attached. You can search for any card with ctrl+F and enter keywords into the box at the upper right corner. Or select from the list Tools>Create cards.
If nodes of different components coincide (occupy the same position in space) we usually equivalence (join) them. This is done in edges panel (shift+F3), where we can specify tolerance, preview and finally equivalence. Connecting with tied contact is usually done for dissimilar meshes.
0