Non Linear Contact In 3 Point Bending
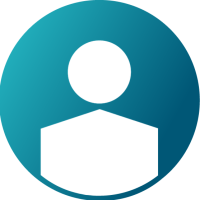
Hi,
I need help with this model. I would like to perform a non-linear analysis on a composite specimen. It's a sandwich panel with honeycomb core, modeled as mat9 ort with two plies of carbon fiber per side.
The main issue is the contact between the punch and the panel, the same as the one with supports. I'm not able to model them correctly. I've thought to use the contact slide but the results does not have sense. I have compared this with real test and the reaction force on the punch is more than 12 times bigger than reality. Looking at the results plot, It's clear that contacts behavior is not acceptable. Can you please help me?
I attach here the .hm file.
Thank you!
Answers
-
Hi,
The laminates were connected to the core with freeze contact. Since both components have matching nodes on the surface the connection can be established with node-to-node connectivity (equivalence in edges panel- F3).
The supports were penetrating the plate and are tied to it with freeze contact (equivalent to gluing the supports to the plate). This is the possible reason for discrepancy compared to test- sliding contact should better approximate the test boundary conditions. Some friction should be able to prevent the plate sliding in Z direction.
Quarter or half symmetry can be used for better computational efficiency and also constrain the plate from sliding.Refer to example OS-E: 0180 3-Point Bending using RBODY
0 -
Thank you for your help,
I'm trying to adjust my model. I need to ask a clarification about the point where you talk about the penetration between the plate and the supports: is the contact based on the shell mesh or do I have to take in account the ticked elements, to avoid intersection? I'll attach a picture to better explain what I'm meaning.
In a previous model I've used slide contact between supports and plys, but the result has been (as you said) a sliding in Z direction, so I changed it into stick contact.
I'll try to use friction to solve the problem.
0 -
For shell elements, the contact and tie search considers the shell thicknesses. This implies that the defined search distance is expected to be the true distance between the shell surfaces facing each other. For example, in the case of shells without offset, if the geometric distance between the two shell surfaces facing each other is 5.0, and the shell thicknesses are 2.0 each, then the actual distance between the shell surfaces facing each other is 3.0. If the Search distance field is now set to 3.0, then the contact is generated as expected (in this scenario, if SRCHDIS is set lower than 3.0, then there is no contact generated).
For more details, please refer to the attached document.
To constrain the plate from sliding:
-use symmetry (refer to 10.3)
-constrain some nodes in the Z DOF0 -
Thank you for you very detailed and precise explanation, it will be very useful!
Can I ask you something that could be a little OT with respect to the topic's title?
Is there a way to orient a MAT9 ORT solid elements? I have tried with Aerospace--> Material Orientation and also with the classic 2D--> Composites --> Material Orientation as possible solutions as I've red here, but they actually don't work.
https://community.altair.com/community?id=community_question&sys_id=7c5644f61b2bd0908017dc61ec4bcb0eTo solve the problem I have changed the engineering constant's arrangement, in the material card definition (E1, E2, E3, G12, ecc..), in order to be congruent with global reference frame in the model.
Is there a smart way to do this? I'm using the last version of Hypermesh 2019
0 -
Stresses are calculated in the material coordinate system. The material coordinate system may be defined as the basic coordinate system (CORDM=0), a user defined system (CORDM = Integer > 0), or the element coordinate system (CORDM=-1).
Edit the PSOLID property and change the CORDM to USER and select the coordinate system which will be the material orientation.
Alternatively, material orientation can be assigned to elements directly with analysis>systems>material orientation. In the model you shared the CHEXA elements are oriented with THETA option. The element angle option for Hexa solid (Theta) is very useful if the material system is changing from element to element.
Make sure to define only one of these options to avoid confusion. Perform a simple 1 element tensile test to verify material orientation.
The like button is a nice way of showing appreciation for the help
/emoticons/default_wink.png' srcset='/emoticons/wink@2x.png 2x' title=';)' width='20' />
0 -
So isn't there a way to verify with vectors on the elements, the x-axis (for example) direction after the user assignment?
Thank you Simon you are the best!!
0 -
There is a tool for material system review: Tools>orientation review>material system
0 -
Really appreciated, thank you!
0