Cylinders contact
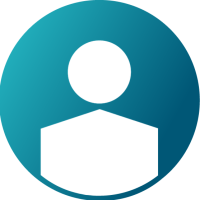
Hi, I would simulate a hertian contact about two cylinders.
I tried to create a smulation but I had some problem about the results and convergence.
In particular I have problems about the contact type (SLIDE, STICK and FREEZE) and track.
I attach the simulation that I created.
Thanks for the advice you will give me.
Answers
-
You would probably need to refine more the contact interfaces to get the analytical Hertz results.
You can work with symmetries to reduce model size.
Concerning convergence, you could request PARAM,NLMON,DISP to check for convergency issues on the fly, as it writes an auxiliary H3D file to follow-up the model run.
OptiStruct documentation provides general info about the contact options.
FREEZE is a tied contact, where parts are bonded and have no relative movement.
Stick is similar to 'infinite' friction after contact is stabilished.
Slide is frictionless contact.
Tracking is more useful when parts are sliding each other (FINITE SLIDING and CONTINUOUS SLIDING), which is not your case. In your case, contact pairs don't change during the analysis.
You might want to request CONTF output, for contact forces/pressures.
0 -
Altair Forum User said:
Hi, I would simulate a hertian contact about two cylinders.
I tried to create a smulation but I had some problem about the results and convergence.
In particular I have problems about the contact type (SLIDE, STICK and FREEZE) and track.
I attach the simulation that I created.
Thanks for the advice you will give me.
Can you please share the fem file ?
0 -
Altair Forum User said:
You would probably need to refine more the contact interfaces to get the analytical Hertz results.
You can work with symmetries to reduce model size.
Concerning convergence, you could request PARAM,NLMON,DISP to check for convergency issues on the fly, as it writes an auxiliary H3D file to follow-up the model run.
OptiStruct documentation provides general info about the contact options.
FREEZE is a tied contact, where parts are bonded and have no relative movement.
Stick is similar to 'infinite' friction after contact is stabilished.
Slide is frictionless contact.
Tracking is more useful when parts are sliding each other (FINITE SLIDING and CONTINUOUS SLIDING), which is not your case. In your case, contact pairs don't change during the analysis.
You might want to request CONTF output, for contact forces/pressures.
Thanks you for the tips.
I will try to refine the mesh and I will use a FREEZE contact.
I would like to simulate Hertz contact about to a gear transmission for this reason one cylinder is much larger than the other.
Altair Forum User said:Can you please share the fem file ?
Yes, of course.
In general the fem's stress are bigger than Hertzian theory.
0 -
FREEZE is not going to give you the right answer here, as it 'ties' all your contact nodes, with zero relative displacement.
You might find an example in OptiStruct Example guide.
You can use full-contact (NL analysis) or a FASTCONTACT approach, like Example 0010.
OS-E: 0010 Wheel Rail Interface using Fast Contact
Demonstrates the use of Fast Contact (FASTCONT). The Wheel Rail interface model is used for meshing using only hexahedral elements.
0