CFD 2D analysis
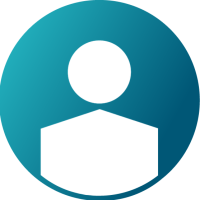
Hi,
I am wondering how to use Atair CFD to conduct 2D airfoil analysis.
And is it possible to do axis symmter for rotorcraft blade anlaysis.
Any example for sources of documentation will be much appreciated.
Thanks,
Jerome.
Best Answer
-
This the validation manual: https://2022.help.altair.com/2022.1/hwcfdsolvers/acusolve/topics/acusolve/introduction_to_the_acusolve_validation.htm
And another involving laminar-to-turbulent transition:
AcuSolve requires one element in the 'thickness' direction for 2D analysis
0
Answers
-
This the validation manual: https://2022.help.altair.com/2022.1/hwcfdsolvers/acusolve/topics/acusolve/introduction_to_the_acusolve_validation.htm
And another involving laminar-to-turbulent transition:
AcuSolve requires one element in the 'thickness' direction for 2D analysis
0 -
acupro_21778 said:
This the validation manual: https://2022.help.altair.com/2022.1/hwcfdsolvers/acusolve/topics/acusolve/introduction_to_the_acusolve_validation.htm
And another involving laminar-to-turbulent transition:
AcuSolve requires one element in the 'thickness' direction for 2D analysis
Hi @acupro , how can a 2D mesh be extruded/dragged in Hyperworks CFD? I'm familiar with the old Acuconsole interface and setting up the case in Hypermesh, where you drag a planar surface mesh in one axis containing one single element layer, with subsequent creation of element face groups for the BC assignment. However, I did not find the drag element utility in HW CFD 2022. Do you have to do it via the volume mesh utility?
0 -
Ingeniorator said:
Hi @acupro , how can a 2D mesh be extruded/dragged in Hyperworks CFD? I'm familiar with the old Acuconsole interface and setting up the case in Hypermesh, where you drag a planar surface mesh in one axis containing one single element layer, with subsequent creation of element face groups for the BC assignment. However, I did not find the drag element utility in HW CFD 2022. Do you have to do it via the volume mesh utility?
Your geometry would represent the extruded solid, with the desired 2D 'thickness' for the eventual single element in the extrusion.
I've attached an example recording showing extrusion meshing. In this case, the extrusion element size yields multiple layers. If you want a single layer, the extrusion element size would just be the thickness in the geometry.
Edge layers are used to define the boundary layer on the extrusion source, which then also get extruded.1 -
acupro_21778 said:
Your geometry would represent the extruded solid, with the desired 2D 'thickness' for the eventual single element in the extrusion.
I've attached an example recording showing extrusion meshing. In this case, the extrusion element size yields multiple layers. If you want a single layer, the extrusion element size would just be the thickness in the geometry.
Edge layers are used to define the boundary layer on the extrusion source, which then also get extruded.Ah, wonderful video, that clears it up. Thank you very much.
0