Problems Modeling Composite Crash Attenuator
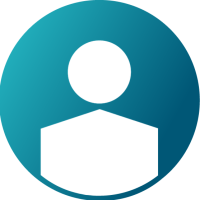
Hi Guys,
i am facing problems modelling a CFRP Nose Cone for Formula Student. When i want to run the simulation i get errors 373 and 1202. Running the Model Checker, it says there are Components missing Material. I haven't assigned the Material, because it should be assigned with the laminate Property. As you can see it also says i'm using Material Law 0 which is not the fact.
Can you help me out?
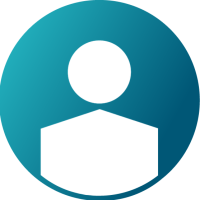
Hi Paul,
first of all thank you for your help. I wouldn't have thought there would be so many errors to fix.
How did you manage to select the areas of the plies without having the composite parts? And do you have any considerations about reducing the computing time? I would need about 3 1/2 hours for one run.
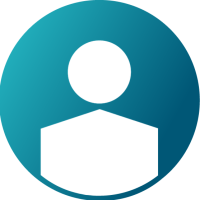

The ply shapes are defined by sets, I didn't do that, you had already defined them in the model (your plies were already defined in your original hm.) Regards runtime, it is related to element size, currently the smallest elements are in the fillets around the bolt recesses at the back of the cone. As it stands, the model I sent back runtime was around 2.5 hrs on my laptop on 6 cores. You can mass scale to 1e-6 time step (/DT/NODA/CST) and the runtime comes down then below 30 minutes. The added mass is around 3%. I just did that and set running. I could quickly see you have a some disconnected mesh in the lower bolt recesses, so you would need to fix those too.
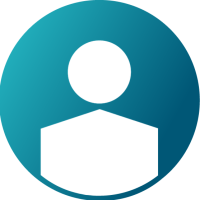
Ah ok, so you just connected the components into one component, right?
To fix the disconnected Mesh, do I just have to use Automesh on these parts of the component again or is there another way to do it?
Thanks Again for your help.
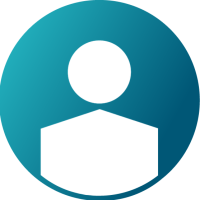

automesh won't connect them if they aren't currently connected, you need to get the 2 sides of the split to match and be equivalenced. But if you automesh both sides with the same settings you should get matching mesh densities. You could then equivalence them manually or with the edges panel (preview equivalence, equivalence)
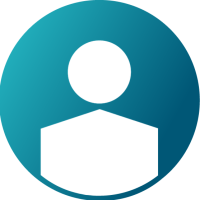
My Problem now is, that i can't remesh the bolt recesses without messing with the mesh of the last part of the nose. Do you think I should re-mesh the whole model?
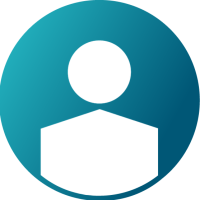

Remeshing everything shouldn't be needed, you should be able to just remesh the area of the box local to the recesses (or the recesses and local surface), but if you have the original geometry, then a full remesh might actually be easier. Either way don't forget to add the new elements back into your plies.
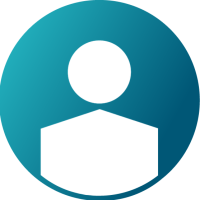
I think i will do the full remesh. How did you delete the Composite Parts from the first model, but kept the meshed shapes?
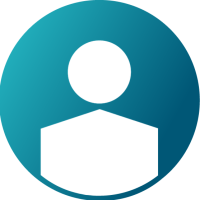

I organised all the elements into the 'Front' component, then deleted the others. If you remesh the crash box, then you will need to recreate the ply shapes based on the new mesh afterwards, the ply shapes are defined by element sets based on the existing mesh, so if you update all the elements those sets won't be valid any more.
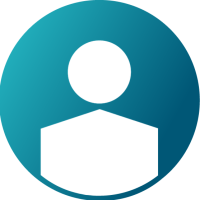
Yes i know, i was just curious how you organised all the elements into the front, because i was thinking of doing it the same way you did.
Also I ran your first model and it takes not really much energy, i think the lower mesh density in the back causes the model to kink, so i will have to increase the mesh density
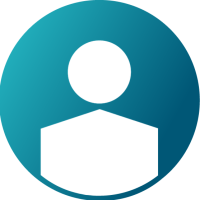

Ok, there are a few things here that aren't correct
First thing, the Part does still need a material assigned to it even though the plies have their own materials, the material assigned at part level is necessary for contact stiffness calculation and timestep calculation.
Second, you are using a 'ply based' /PROP/TYPE51 laminate property, but you have multiple parts referencing that /PROP, more like what you would have for a zone based laminate. The issue then is you have Parts, that reference a laminate, that reference plies, where the elements of those plies are not in that part.
Either Zone based or Ply based is ok, but you need to pick one or the other!
With Ply based, you should put all of your composite elements in one part, the laminate/plies sort out the different areas.
In attached, this now begins to run (i.e. starter completes without errors). I haven't checked beyond that so there will likely be more to do! but fixes I put in are:
Delete all Composite Parts except 'Front'
Deleted the additional unused /STACK card
Added the ply 11 to the laminate (it had been left out)
Assign Twill Mat to Part
Updated orientation on /PROP/TYPE51 to prevent normals being perpendicular to back plate
Modified Tied interface to Spotflag 27 (to avoid incompatible kinematic conditions with the rigid)
Added search distance for Tied interface
Added Ignore flag to tied interface
Good Luck!
Paul
Ok, there are a few things here that aren't correct
First thing, the Part does still need a material assigned to it even though the plies have their own materials, the material assigned at part level is necessary for contact stiffness calculation and timestep calculation.
Second, you are using a 'ply based' /PROP/TYPE51 laminate property, but you have multiple parts referencing that /PROP, more like what you would have for a zone based laminate. The issue then is you have Parts, that reference a laminate, that reference plies, where the elements of those plies are not in that part.
Either Zone based or Ply based is ok, but you need to pick one or the other!
With Ply based, you should put all of your composite elements in one part, the laminate/plies sort out the different areas.
In attached, this now begins to run (i.e. starter completes without errors). I haven't checked beyond that so there will likely be more to do! but fixes I put in are:
Delete all Composite Parts except 'Front'
Deleted the additional unused /STACK card
Added the ply 11 to the laminate (it had been left out)
Assign Twill Mat to Part
Updated orientation on /PROP/TYPE51 to prevent normals being perpendicular to back plate
Modified Tied interface to Spotflag 27 (to avoid incompatible kinematic conditions with the rigid)
Added search distance for Tied interface
Added Ignore flag to tied interface
Good Luck!
Paul