Can I add symmetry manufacturing constraint in Ply Stacking Sequence Optimization ?
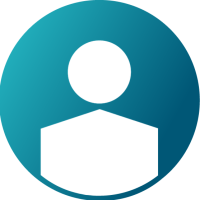

In DSHUFFLE card, we can select three options including MAXSUCC, PAIR ,CORE/COVER(see figure attached). But, the plies of laminate structure is requested to be symmetric.How can I add this constraint in shuffle optimization ??
My firend ask me to test what will happen if 'PAIR 0 90 SAME' in DSHUFFLE card is added in .fem file. But Solver FAILED, the error message is ' BALANCE and PAIR constraints are only valid for 45.0 and -45.0 orientations at this point.' Hope someone can help me, thanks very much!
Find more posts tagged with
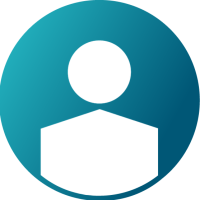

Hi HuangZhou,
I don't think it is possible to make the laminate symmetry at this stage.
I will check with a sample model if making the laminate type symmetry will make any difference in the number plies and I will update to you the same soon.
Thank you very much! If I can't restrict the laminate's symmetry in shuffle optimization, is it mean I needn't(or can't )do shuffle optimization for symmetric laminate structure?
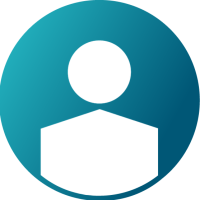

Hi HuangZhou,
You can make the laminate symmetry using laminate options. But this will double the thickness.
1) Try this, select all plies in model browser and reduce the thickness of the plies by half. So, if the individual ply thickness is 1.. make it to 0.5.
2) Change the laminate option to symmetry
3) now, run shuffling optimization and check the results if they are satifying the overall design constraints.
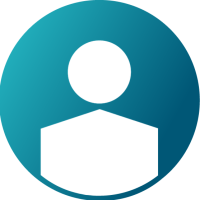

Hi HuangZhou,
You can make the laminate symmetry using laminate options. But this will double the thickness.
1) Try this, select all plies in model browser and reduce the thickness of the plies by half. So, if the individual ply thickness is 1.. make it to 0.5.
2) Change the laminate option to symmetry
3) now, run shuffling optimization and check the results if they are satifying the overall design constraints.
Good method! And I have tested another method:
In phase 1, I define laminate as symmetry, so the there are 8 super-plies in result which come in pairs in thickness.
In phase 2, I change smear to symmetry and delect extra 4 plies.
In phase3, the laminate is symmetry, I can run shuffling optimization.
But I have another question which puzzles me. Your method (or OptiStruct Optimization method for Composite) means we don't care about the sequence of laminate in Size Optimization ,and in the next Shuffling Optimization we only optimize the sequence. Why can we separate the two steps ??? Is it possile to get better results if phase2 and phase 3 are combined together?
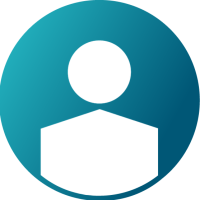

Hi,
Sorry for a late reply.
The basic idea of the three phase composite optimization is to generate a concept for the structure which uses composites from scratch.
One can eliminate the last phase by having custom stacking sequence.
Hi HuangZhou,
I don't think it is possible to make the laminate symmetry at this stage.
I will check with a sample model if making the laminate type symmetry will make any difference in the number plies and I will update to you the same soon.