Why 3D elements have only 3 Degrees of freedom?
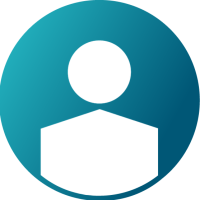

Sir,
Why 3D elements have only 3 Degrees of freedom? I referred our Book- Practical Aspects FEA, they say 'after rod (1D), paper (2D), imagin a (wooden) duster (3D), can you EASILY twist it?,.... Hence only 3 d.o.f.s NO ROTATIONAL D.O.F.s '
My query is 'what about a solid ductile metal duster tested with a torsion tester (now not to worry about the capacity)?' Now what if it could twist EASILY?
Answers
-
Altair Forum User said:
Sir,
Why 3D elements have only 3 Degrees of freedom? I referred our Book- Practical Aspects FEA, they say 'after rod (1D), paper (2D), imagin a (wooden) duster (3D), can you EASILY twist it?,.... Hence only 3 d.o.f.s NO ROTATIONAL D.O.F.s '
My query is 'what about a solid ductile metal duster tested with a torsion tester (now not to worry about the capacity)?' Now what if it could twist EASILY?
No, 3D element have NO DoF! The exact words are : 3D element's nodes have only 3 DoF.
No rotational DoF at node, but you can analyse the torsional behavior of a part with 3D element no problem.
Maybe have a look (again) at some FE textbooks ?
0 -
Hi
I had exactly same questions when i was in university and no teacher told me answer, unfortunately my fe textboooks just say that brick has 3 dofs/node, shell 6dofs/node,... but do not explain
then i have to imagine (actually similar to when i was processing of mechanical parts):
- when I lathe a shaft (ROD), i have to position one end fully in a clamper (like a tube), so ROD need 6 dofs/node to be fully constrained
- when I punch a sheet (SHELL), i have to position one corner with 5 dofs and one other corner 1 dof (in-plane rotation), so SHELL has 5 dofs/node, remain in-plane rotation dof is constrained by adjacent node, so you never let 2 shell elements connect together by only 1 node (cannot transfer moment). But some solvers may provide particular SHELL has fully 6dofs/node, like CQUADR in nastran/optistruct
- when I mill a block (BRICK), i have to position 3 faces so it cannot move in 3 directions, after position 3 faces then it cannot rotation around 3 axles also because each plane (face) constrained rotation dofs. so BRICK have 3 translation-dofs/node and it is enough to transfer moment
put more dofs in to a fully position part (element) will make it over-constrained (too stiff)
and be careful when connect 1d to 2d, 2d to 3d or 1d to 3d, you have to take into account all dofs have to be constrained
0 -
The question is not why does it have only 3, it is more a question of why have we formulated it to have only 3 dof.
Solid components generally cannot be subjected to very high bending or torsion, hence, solid elements have been formulated with 3 translational dofs and no rotational dofs.If you are simulating a special case with a material that requires 6 dof elements, I think, you will have to use midsurfacing and shell or some other work around,
0 -
Altair Forum User said:
The question is not why does it have only 3, it is more a question of why have we formulated it to have only 3 dof.
Solid components generally cannot be subjected to very high bending or torsion, hence, solid elements have been formulated with 3 translational dofs and no rotational dofs.If you are simulating a special case with a material that requires 6 dof elements, I think, you will have to use midsurfacing and shell or some other work around,Hi ,
By Midsurfacing you mean higher order elements right?
For example use of Brick element with higher orderor order 2
yours sincerely,
kartik
0 -
Hello
No by Midsurface he means that you need to generate the midsurface of the 3D component and then shell mesh and then apply the conditions to simulate the special case.
Thank you
0